Transmission structure of nipper of comber
A transmission structure and combing machine technology, applied in the direction of combing machines, textiles, papermaking, fiber processing, etc., can solve the problem of unsatisfactory nipper transmission mechanism and mode, affecting the service life of the action precision device, and the inertia of mechanical action Large and other problems, to achieve the effect of simple structure, improved driving power, and easy processing
- Summary
- Abstract
- Description
- Claims
- Application Information
AI Technical Summary
Problems solved by technology
Method used
Image
Examples
Embodiment 1
[0028] A transmission structure of the nipper of a combing machine. A fulcrum of the nipper 12 is rotatably connected to a support rod 11 at the lower part which is rotatably connected to the base. The rotating wheel 1 of the servo motor mechanism passes through the eccentric wheel 18 to eccentrically rotate and connect the nipper. Another fulcrum for 12. The servomotor mechanism is two servomotors, wherein one A servomotor 7 meshes with the planet carrier gear 9 of a planetary gear through the A servomotor gear 6, and the other B servomotor 8 meshes with the sun gear 10 of the planetary gear. The rear planetary gear 4 is meshed, and the front planetary wheel 3 is meshed with the output gear 2, and the output gear 2 is coaxially connected with the rotating wheel 1.
[0029] A servo motor 7 and B servo motor 8 are synthesized on an output gear 2 through a planetary gear mechanism, which not only improves the power to drive the nipper 12, but also coordinates the two servo motor...
Embodiment 2
[0031] A transmission structure of the nipper of a combing machine. A fulcrum of the nipper 12 is rotatably connected to a support rod 11 at the lower part which is rotatably connected to the base. The rotating wheel 1 of the servo motor mechanism passes through the eccentric wheel 18 to eccentrically rotate and connect the nipper. Another fulcrum for 12. The servo motor mechanism is that the A servo motor gear 6 and the B servo motor gear 9 of the two servo motors are all meshed with the coaxial output gear 2 of the rotating wheel 1 .
[0032] A servo motor 7 and B servo motor 8 two servo motors directly mesh to drive an output gear 2, and the rotation of the output gear 2 rotates through the eccentric wheel 18 to connect another fulcrum of the nipper 12 to realize the swing operation of the nipper 12. The two servo motors have both improved the power to drive the nipper 12, and are driven by computer programming to drive and change the rotational speed of the output gear 2, ...
PUM
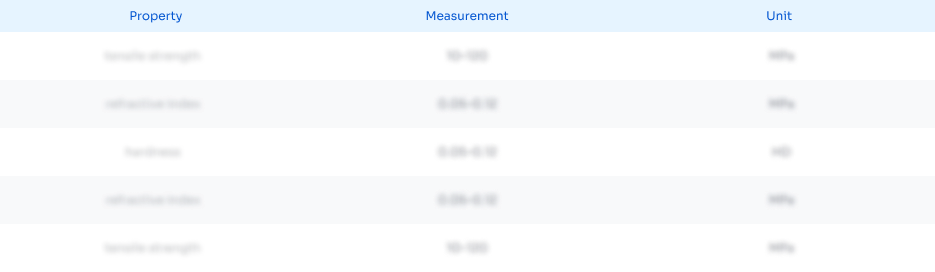
Abstract
Description
Claims
Application Information

- R&D
- Intellectual Property
- Life Sciences
- Materials
- Tech Scout
- Unparalleled Data Quality
- Higher Quality Content
- 60% Fewer Hallucinations
Browse by: Latest US Patents, China's latest patents, Technical Efficacy Thesaurus, Application Domain, Technology Topic, Popular Technical Reports.
© 2025 PatSnap. All rights reserved.Legal|Privacy policy|Modern Slavery Act Transparency Statement|Sitemap|About US| Contact US: help@patsnap.com