Construction method of furnace cavity liner of garbage incinerator
A waste incinerator and furnace lining technology, which is applied in the combustion method, incinerator, combustion type, etc., can solve the problems of waste, matrix deformation, high cost, save use and maintenance costs, and improve wear resistance and thermal conductivity. , Excellent thermal shock resistance
- Summary
- Abstract
- Description
- Claims
- Application Information
AI Technical Summary
Problems solved by technology
Method used
Examples
Embodiment 1
[0013] The furnace lining construction method of the garbage incinerator of the present invention includes the steps of batching, ramming construction, anchoring and drying;
[0014] In the batching step, the ramming material comprises the following components by mass percentage: Fe 2 o 3 1.2%, Al 2 o 3 10%, SiC80%, silicate coupling agent 8.8%; silicate in silicate coupling agent includes aluminum, iron, calcium, magnesium, potassium, sodium and other silicates, which can reach this level during use. The desired effect of the invention.
[0015] In the ramming construction step, the ramming should be carried out continuously in blocks, and the ramming should be layered once to the design thickness, and each layer should be rammed 3-5 times.
[0016] In the anchoring step of this embodiment, the total height of the membrane wall of the waste incinerator in this embodiment is about 16.5 meters, and along the height direction of the membrane wall from the lower header (inc...
Embodiment 2
[0027] The furnace lining construction method of the garbage incinerator of the present invention includes the steps of batching, ramming construction, anchoring and drying;
[0028] In the batching step, the ramming material comprises the following components by mass percentage: Fe 2 o 3 1.5%, Al 2 o 3 7%, SiC74.5%, silicate coupling agent 17%
[0029] In the ramming construction step, the ramming should be carried out continuously in blocks, and the ramming should be layered once to the design thickness, and each layer should be rammed 3-5 times.
[0030] In this embodiment, conventional anchoring methods are used for anchoring.
[0031] In the drying step, the drying temperature is a constant temperature of 250°C.
[0032] After this embodiment was put into use for 36 months, it was tested that the ratio of ingredients, anchoring method and drying temperature used in this embodiment have more prominent advantages compared with the existing technology, but it is more ...
Embodiment 3
[0034] The furnace lining construction method of the garbage incinerator of the present invention includes the steps of batching, ramming construction, anchoring and drying;
[0035] In the batching step, the ramming material comprises the following components by mass percentage: Fe 2 o 3 1.3%, Al 2 o 3 8.7%, SiC 85%, silicate coupling agent 5%;
[0036] In the ramming construction step, the ramming should be carried out continuously in blocks, and the ramming should be layered once to the design thickness, and each layer should be rammed 3-5 times.
[0037] In this embodiment, conventional anchoring methods are used for anchoring.
[0038] In the drying step, the drying temperature is a constant temperature of 250°C.
[0039] After this embodiment was put into use for 36 months, it was tested that the ratio of ingredients, anchoring method and drying temperature used in this embodiment have more prominent advantages compared with the existing technology, but it is more...
PUM
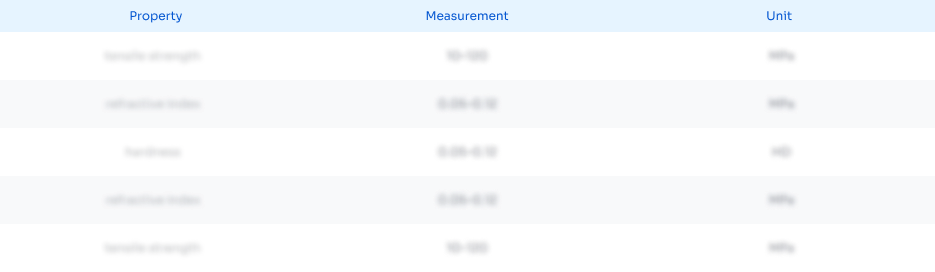
Abstract
Description
Claims
Application Information

- Generate Ideas
- Intellectual Property
- Life Sciences
- Materials
- Tech Scout
- Unparalleled Data Quality
- Higher Quality Content
- 60% Fewer Hallucinations
Browse by: Latest US Patents, China's latest patents, Technical Efficacy Thesaurus, Application Domain, Technology Topic, Popular Technical Reports.
© 2025 PatSnap. All rights reserved.Legal|Privacy policy|Modern Slavery Act Transparency Statement|Sitemap|About US| Contact US: help@patsnap.com