Polyacrylic ester thickener and preparation method thereof
A polyacrylate and thickener technology, applied in textiles, papermaking, fiber processing, etc., can solve problems such as affecting the appearance, affecting the audio resonance frequency of the speaker, and unable to obtain higher sound quality output, and improving the appearance and movement space. The effect of increased resistance, good viscosity binding ability
- Summary
- Abstract
- Description
- Claims
- Application Information
AI Technical Summary
Problems solved by technology
Method used
Examples
Embodiment 1
[0028] (1) The weight ratio of raw material components is: %
[0029] Sodium lauryl sulfate 0.3
[0030] Alkylphenol polyoxyethylene ether 0.5
[0031] Methacrylic acid 12
[0032] Ethyl acrylate 18
[0033] N-methacrylamide 0.5
[0034] Synergist 0.5
[0035] Ammonium persulfate 0.6
[0036] Deionized water 67.6
[0037] One of the synergists is sodium vinyl sulfonate.
[0038] (2) The preparation method is:
[0039] (1) Add the aqueous solution of compound emulsifier in the reactor according to the weight formula: sodium lauryl sulfate 0.3, alkylphenol polyoxyethylene ether 0.6, deionized water 30, stir evenly;
[0040] (2) Add 1 / 5 of the monomer mixture: methacrylic acid 12, ethyl acrylate 18, 1 / 5 (initiator + synergist + N-methacrylamide) mixed aqueous solution: ammonium persulfate 0.6, synergistic Agent 0.5, N-methacrylamide 0.5, the balance of deionized water, heat up to 65 ℃, keep warm for 20min;
[0041] (3) Raise the temperature to 85°C, add the remaining in...
Embodiment 2
[0043] (1) The weight ratio of raw material components is: %
[0044] Sodium lauryl sulfate 0.3
[0045] Alkylphenol polyoxyethylene ether 0.5
[0046] Methacrylic acid 8
[0047] Ethyl acrylate 22
[0048] N-methacrylamide 0.8
[0049]Synergist 2.5
[0050] Ammonium persulfate 0.5
[0051] Deionized water 65.4
[0052] One of the synergists is sodium propenyl sulfonate.
[0053] (2) The preparation method is:
[0054] (1) Add the aqueous solution of compound emulsifier in the reactor by weight formula: sodium lauryl sulfate 0.3, alkylphenol polyoxyethylene ether 0.5, deionized water 30, stir evenly;
[0055] (2) Add 1 / 5 of the monomer mixture: methacrylic acid 8, ethyl acrylate 22, 1 / 5 (initiator + synergist + N-methacrylamide) mixed aqueous solution: ammonium persulfate 0.5, synergistic Agent 2.5, N-methacrylamide 0.8, the balance of deionized water, heat up to 75°C, keep warm for 40min;
[0056] (3) Raise the temperature to 80°C, drop the remaining aqueous initiat...
Embodiment 3
[0058] (1) The weight ratio of raw material components is: %
[0059] Sodium lauryl sulfate 0.3
[0060] Alkylphenol polyoxyethylene ether 0.5
[0061] Methacrylic acid 10
[0062] Ethyl acrylate 20
[0063] N-methacrylamide 2.8
[0064] Synergist 4.5
[0065] Ammonium persulfate 0.5
[0066] Deionized water 61.4
[0067] The synergist among them is 2-acrylamide-2-methylpropanesulfonic acid.
[0068] (2) The preparation method is:
[0069] (1) Add the aqueous solution of compound emulsifier in the reactor by weight formula: sodium lauryl sulfate 0.3, alkylphenol polyoxyethylene ether 0.5, deionized water 30, stir evenly;
[0070] (2) Add 1 / 5 of the monomer mixture: methacrylic acid 10, ethyl acrylate 20, 1 / 5 (initiator + synergist + N-methacrylamide) mixed aqueous solution: ammonium persulfate 0.5, synergistic Agent 4.5, N-methacrylamide 2.8, the balance of deionized water, heat up to 80°C, keep warm for 30min;
[0071] (3) Raise the temperature to 85°C, add the rema...
PUM
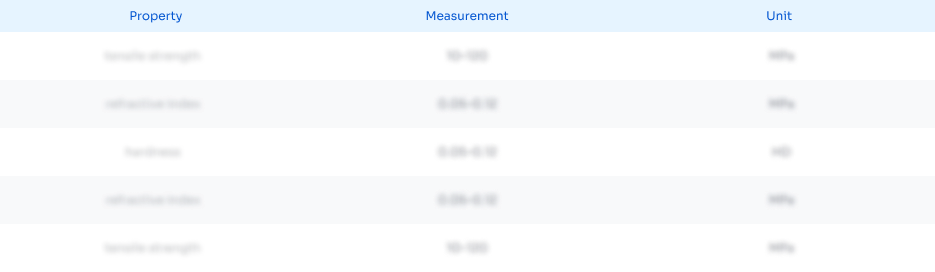
Abstract
Description
Claims
Application Information

- R&D
- Intellectual Property
- Life Sciences
- Materials
- Tech Scout
- Unparalleled Data Quality
- Higher Quality Content
- 60% Fewer Hallucinations
Browse by: Latest US Patents, China's latest patents, Technical Efficacy Thesaurus, Application Domain, Technology Topic, Popular Technical Reports.
© 2025 PatSnap. All rights reserved.Legal|Privacy policy|Modern Slavery Act Transparency Statement|Sitemap|About US| Contact US: help@patsnap.com