Process for producing industrial fluorene by coal tar wash oil
A technology for production industry and process method, applied in the directions of organic chemistry, absorption purification/separation, crystallization purification/separation, etc., can solve the problems of low yield of industrial fluorene products, low level of automation, high power consumption, and achieve easy control and adjustment. , the effect of high level of automation and low power consumption
- Summary
- Abstract
- Description
- Claims
- Application Information
AI Technical Summary
Problems solved by technology
Method used
Image
Examples
Embodiment 1
[0012] Example 1, such as figure 2 Shown: the present invention uses coal tar washing oil to remove the heavy washing oil after components such as naphthalene, methylnaphthalene, dimethylnaphthalene, acenaphthene as raw material and sends into the front tower 201, and in the tower, normal pressure or decompression refining After distillation, the fluorene front cut is cut in the tower top condensing cooler 103, and this part of the fluorene front cut is sent as a by-product. The material at the bottom of the tower is sent to the fluorene tower 205 by the fluorene tower feed pump 204, and the bottom of the front tower 201 and the fluorene tower 205 are heated by the reboilers 202 and 208. After extracting the fluorene fraction from the bottom, the residual oil is sent outside. Cut the fluorene fraction containing about 60% fluorene at the top of the tower. The fluorene fraction enters the reflux tank 104 after being cooled by the condensing cooler 206 at the top of the fluor...
Embodiment 2
[0015] Embodiment 2, as attached image 3 Shown, process method of the present invention also can adopt a tower type continuous rectification production unit, and its flow process is:
[0016] The heavy oil washing raw material enters the rectification tower 301, and is rectified in the tower under normal or reduced pressure, and the heavy residual oil is extracted from the bottom of the tower and sent out. The fluorene pre-fraction is cut from the top of the tower, and after passing through the condensing cooler 103, the fluorene pre-fraction enters the reflux tank 104, and then a part of the fluorene pre-fraction is sent to the tower for reflux through the reflux pump 207, and the rest of the fluorene pre-fraction is sent out. The fluorene fraction is cut from the discharge side line, cooled by the fluorene fraction cooler 304, and the treatment process of the cooled fluorene fraction is as in the previous embodiment 1. Similarly, the fluorene-rich residual oil can be retur...
PUM
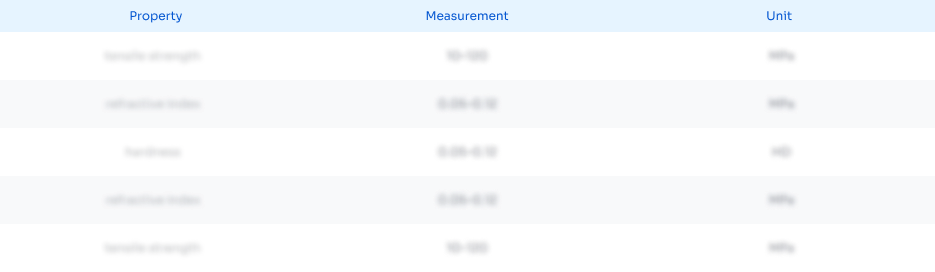
Abstract
Description
Claims
Application Information

- R&D
- Intellectual Property
- Life Sciences
- Materials
- Tech Scout
- Unparalleled Data Quality
- Higher Quality Content
- 60% Fewer Hallucinations
Browse by: Latest US Patents, China's latest patents, Technical Efficacy Thesaurus, Application Domain, Technology Topic, Popular Technical Reports.
© 2025 PatSnap. All rights reserved.Legal|Privacy policy|Modern Slavery Act Transparency Statement|Sitemap|About US| Contact US: help@patsnap.com