Upward forming method of thermal dip-coating copper covered steel and upward forming device thereof
A forming method and technology of copper-clad steel, applied in the production of copper-clad steel by hot dip coating, and the field of copper-clad steel production, which can solve the problems of disorderly vibration, accelerated inlet and outlet contact wear, long soaking time of steel core rods, etc.
- Summary
- Abstract
- Description
- Claims
- Application Information
AI Technical Summary
Problems solved by technology
Method used
Image
Examples
Embodiment Construction
[0017] The hot-dip coated copper-clad steel upward forming method of the present invention, the key is to enter the preheated steel rod from the bottom of the crucible, and then dip-coat it from the copper water in the crucible and then pull it out vertically from the top of the crucible. The specific control method of other parameters is further described in detail as follows:
[0018] 1. The preheating temperature of the steel rod is inversely proportional to the electrical conductivity. The corresponding preheating temperature of 21-70% IACS is 500-60°C. It is not possible to obtain a CS wire with a copper coating ratio of 20% (about 30% IACS). Only by heating the steel wire to increase its temperature and reduce the amount of heat exchange per unit time can the amount of copper coating be reduced. In this way, a CS line with a low covering ratio can be obtained. If the wire is dip-coated for the second time, a CS wire with a copper-clad steel cladding ratio of 80% can be ...
PUM
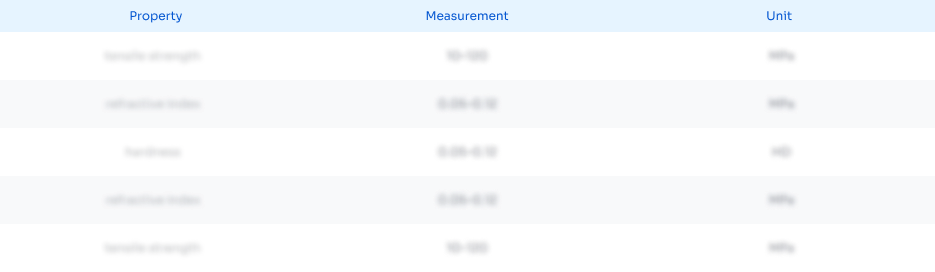
Abstract
Description
Claims
Application Information

- R&D Engineer
- R&D Manager
- IP Professional
- Industry Leading Data Capabilities
- Powerful AI technology
- Patent DNA Extraction
Browse by: Latest US Patents, China's latest patents, Technical Efficacy Thesaurus, Application Domain, Technology Topic, Popular Technical Reports.
© 2024 PatSnap. All rights reserved.Legal|Privacy policy|Modern Slavery Act Transparency Statement|Sitemap|About US| Contact US: help@patsnap.com