Intrinsic non-net secondary cementite steel and application method thereof
A technology of cementite steel and carbon steel, applied in the field of high carbon steel and bearing steel, to achieve the effect of simple spheroidizing process, shortening spheroidizing time and increasing hardness
- Summary
- Abstract
- Description
- Claims
- Application Information
AI Technical Summary
Problems solved by technology
Method used
Image
Examples
Embodiment example 1
[0032] Implementation case 1, an intrinsic non-network secondary cementite steel, according to the weight percentage, the chemical composition of the cementite steel is shown in Table 1:
[0033] Table 1 chemical composition
[0034] the element
[0035] figure 1 It shows that the material is vacuum-heated at 1100°C for 4 hours and furnace-cooled for 4 hours after being rolled in a vacuum capacity. There is no reticular cementite in the structure, and there are flocculent and dispersed precipitates between the cementite strips. See figure 1 -b, figure 2 It is a TEM photo, which more clearly shows the distribution of dispersed precipitates and cementite strips, and is observed and analyzed by a high-resolution electron microscope (see image 3 ), these precipitates are a kind of AM decomposition. This kind of structure is easy to spheroidize. After heating at 850°C for 15 minutes and cooling at 1°C / min to 750°C, the ideal spheroidized structure is obtained. See ...
Embodiment example 2
[0036] Implementation case 2: An intrinsic non-network secondary cementite steel, according to the weight percentage, the chemical composition of the cementite steel is shown in Table 1:
[0037] Table 1 chemical composition
[0038] the element
[0039] The chemical composition is the same as that of Example 1. The material is subjected to conventional heat quenching and tempering treatment. The specific process is heating (salt bath furnace) to 840±10°C for heat preservation, tempering temperature is 155±5°C, and tempering for 2-2.5 hours. Figure 5 It is a quenched structure, and the structure is martensite and retained austenite plus residual carbide. Image 6 In comparison with the structure of GCr15 after the same heat treatment, it can be seen from the comparison that the structure of the present invention is obviously finer, and the amount of retained austenite is also relatively small. These characteristics are very beneficial to improving the performance of...
Embodiment example 3
[0040] Implementation case 3, an intrinsic non-network secondary cementite steel, according to the weight percentage, the chemical composition of the cementite steel is shown in Table 2:
[0041] Table 2 chemical composition
[0042] the element
[0043] The composition of Example 1 contains Al, which may bring difficulties to the control of inclusions in smelting. The composition given in Example 3 does not contain Al, but the content of Si is increased to more than 1.0. Figure 8 The results given show that there is still no reticular cementite in the as-cast structure.
PUM
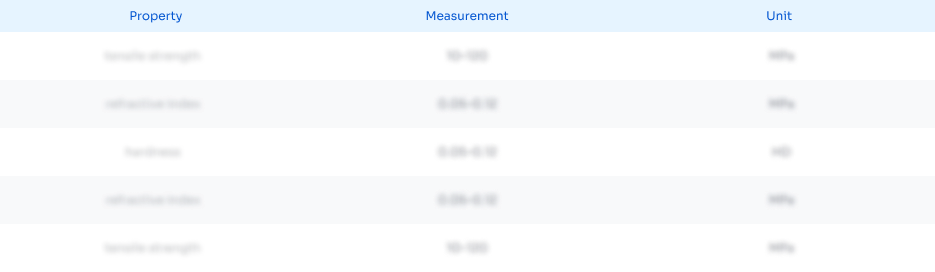
Abstract
Description
Claims
Application Information

- R&D
- Intellectual Property
- Life Sciences
- Materials
- Tech Scout
- Unparalleled Data Quality
- Higher Quality Content
- 60% Fewer Hallucinations
Browse by: Latest US Patents, China's latest patents, Technical Efficacy Thesaurus, Application Domain, Technology Topic, Popular Technical Reports.
© 2025 PatSnap. All rights reserved.Legal|Privacy policy|Modern Slavery Act Transparency Statement|Sitemap|About US| Contact US: help@patsnap.com