Inner-complex cooling pipe and method for producing the same
A manufacturing method and technology for cooling pipes, applied to tubular elements, lighting and heating equipment, heat exchange equipment, etc., can solve problems such as waste of manpower and material resources, unfavorable air, water circulation, and increased material costs, and reduce personnel , Avoid short circuit phenomenon, reduce production cost
- Summary
- Abstract
- Description
- Claims
- Application Information
AI Technical Summary
Problems solved by technology
Method used
Image
Examples
Embodiment 1
[0030] The finished product specification is a four-channel composite copper tube, the outer diameter of the outer tube: 12mm, the inner diameter: 8mm; the outer diameter of the inner tube is 8mm, the inner diameter: 6mm.
[0031] 1. Lining core garden drawing: Lining the red copper blank tube with a state of Y, a grade of T2, a specification of φ38×3.0mm, and a length of about 4.5 meters. The function of the lining is correction; the function of the empty drawing is to Diameter reduction, deviation correction. The two processes of lining drawing and empty drawing are carried out in a cycle until the blank tube is drawn to φ21×2.60mm, that is, the inner diameter is φ15.8mm.
[0032] 2. Grooving of the sleeve mold: the copper blank tube of φ21×2.60mm obtained in step 1, that is, the copper blank tube with an inner diameter of φ15.8mm, is drawn by the sleeve mold and grooved, and drawn in eight times to form an inner four-slot tube with an outer diameter of φ12 and an inner diam...
Embodiment 2
[0038] The finished product specification is a six-channel composite copper tube, the outer diameter of the outer tube: 16mm, inner diameter: 10mm; the outer diameter of the inner tube is 10mm, inner diameter: 6.7mm.
[0039] 1. Lining core garden drawing: Lining the red copper blank tube with a state of Y, a grade of T2, a specification of φ40×4.2mm, and a length of about 5 meters. The function of the lining is correction; the function of the empty drawing is to Diameter reduction, deviation correction. The two processes of lining drawing and empty drawing are carried out in a cycle until the blank tube is drawn to φ28×4.0mm, that is, the inner diameter is φ20mm.
[0040] 2. Grooving of the cover mold: the φ28×4.0 obtained in step 1, that is, the red copper blank tube with an inner diameter of φ20mm is drawn into the grooving of the sleeve mold, and drawn in six times to form an inner six-groove tube with an outer diameter of φ16 and an inner diameter of φ10 for use.
[0041...
PUM
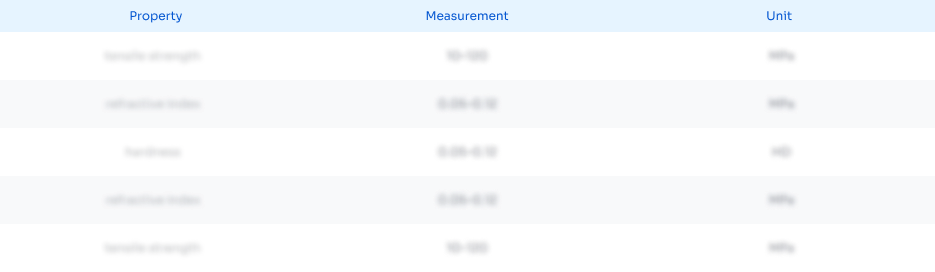
Abstract
Description
Claims
Application Information

- R&D
- Intellectual Property
- Life Sciences
- Materials
- Tech Scout
- Unparalleled Data Quality
- Higher Quality Content
- 60% Fewer Hallucinations
Browse by: Latest US Patents, China's latest patents, Technical Efficacy Thesaurus, Application Domain, Technology Topic, Popular Technical Reports.
© 2025 PatSnap. All rights reserved.Legal|Privacy policy|Modern Slavery Act Transparency Statement|Sitemap|About US| Contact US: help@patsnap.com