Manufacturing method of plastic fuel tank
A manufacturing method and fuel tank technology are applied in the manufacturing field of plastic fuel tanks, which can solve the problems of low production efficiency of single-station blow molding machines, reduce investment in tooling equipment and production space, reduce energy consumption, and improve drying effect. Effect
- Summary
- Abstract
- Description
- Claims
- Application Information
AI Technical Summary
Problems solved by technology
Method used
Image
Examples
Embodiment Construction
[0021] The manufacture method of plastic fuel tank of the present invention comprises the following steps:
[0022] (1) Inhale high-density polyethylene, adhesive material, barrier material, and flash material into the storage tanks with sufficient reserves through the vacuum feeding system;
[0023] (2) Dry the barrier material and flash material particles, and control the drying temperature at 90±5°C;
[0024] (3) Use six special extruders with automatic weighing control to pump out qualitative and quantitative melt materials, and continuously extrude a 6-layer parison downward through the co-extrusion die head, and the parison is a cylinder with an open lower end Shaped and vertically hung under the die head, the thickness ratio of each layer from the inside to the outside is: high-density polyethylene: adhesive material: barrier material: adhesive material: recycled material: high-density polyethylene = 37:1.5 : 2: 1.5: 46: 12; Add black color masterbatch to the outer lay...
PUM
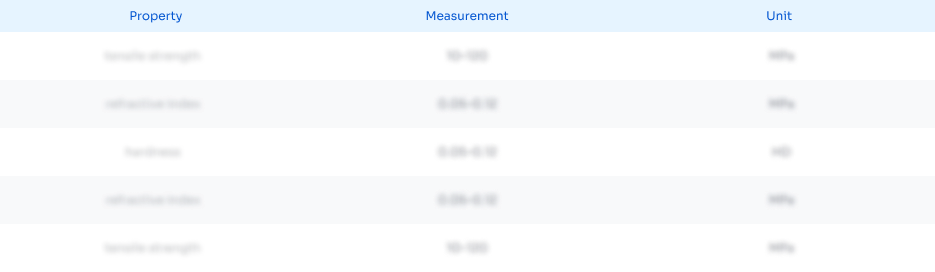
Abstract
Description
Claims
Application Information

- R&D Engineer
- R&D Manager
- IP Professional
- Industry Leading Data Capabilities
- Powerful AI technology
- Patent DNA Extraction
Browse by: Latest US Patents, China's latest patents, Technical Efficacy Thesaurus, Application Domain, Technology Topic, Popular Technical Reports.
© 2024 PatSnap. All rights reserved.Legal|Privacy policy|Modern Slavery Act Transparency Statement|Sitemap|About US| Contact US: help@patsnap.com