Method for improving degree of graphitization of graphite material
A technology of graphitization degree and graphite material, applied in the field of structural modification of inorganic carbon materials, can solve the problems of large spacing between graphite wafers, small average crystallite size, complex processing equipment, etc. Large, simple handling equipment
- Summary
- Abstract
- Description
- Claims
- Application Information
AI Technical Summary
Problems solved by technology
Method used
Image
Examples
Embodiment 1
[0010] Put the graphite powder with a low degree of graphitization into a glass bottle at room temperature, and then place the glass bottle in 60 In the γ-ray irradiation room of Co, the γ-ray irradiation dose rate is 6.0×10 3 Gy / h, the irradiation dose is 2×10 6 The graphite material was irradiated with γ-rays under the condition of Gy, and the irradiation time was 340h, and the degree of graphitization increased from 75% to 81%.
Embodiment 2
[0012] Put the graphite powder with a low degree of graphitization into a glass bottle at room temperature, and then place the glass bottle in 60 In the γ-ray irradiation room of Co, the γ-ray irradiation dose rate is 3.6×10 3 Gy / h, the irradiation dose is 1×10 6 The graphite material was irradiated with γ-rays under the condition of Gy, and the irradiation time was 278h, and the degree of graphitization increased from 75% to 79%.
Embodiment 3
[0014] Put the graphite powder with a low degree of graphitization into a glass bottle at room temperature, and then place the glass bottle in 60 In the γ-ray irradiation room of Co, the γ-ray irradiation dose rate is 0.6×10 3 Gy / h, the irradiation dose is 0.6×10 6 Under the condition of Gy, the graphite material is irradiated with γ-rays, and the irradiation time is 1×10 3 h, the degree of graphitization increased from 75% to 78%.
[0015] A small amount of irradiated graphite powder in Example 1 was taken for X-ray diffraction (XRD) analysis, and compared with graphite powder not irradiated. Through X-ray diffraction analysis, it is found that the graphite wafer spacing of graphite powder is reduced from 0.33756nm before irradiation treatment to 0.33706nm after irradiation treatment. According to the formula for calculating the degree of graphitization proposed by Maire and Mering, the graphite powder The degree of graphitization increases from 74.88% before irradiation t...
PUM
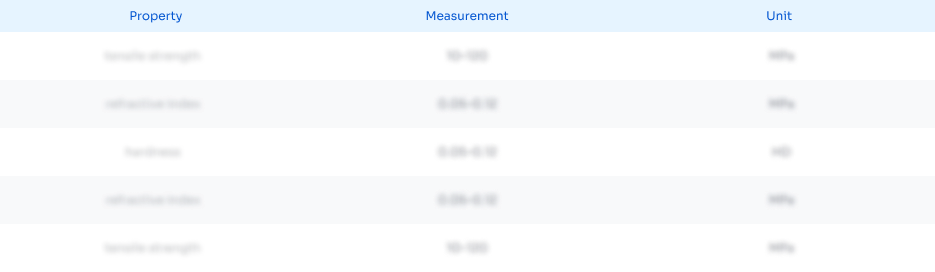
Abstract
Description
Claims
Application Information

- R&D
- Intellectual Property
- Life Sciences
- Materials
- Tech Scout
- Unparalleled Data Quality
- Higher Quality Content
- 60% Fewer Hallucinations
Browse by: Latest US Patents, China's latest patents, Technical Efficacy Thesaurus, Application Domain, Technology Topic, Popular Technical Reports.
© 2025 PatSnap. All rights reserved.Legal|Privacy policy|Modern Slavery Act Transparency Statement|Sitemap|About US| Contact US: help@patsnap.com