Method for molding via hole of printed circuit board
A printed circuit board and molding method technology, applied in the direction of electrical connection formation of printed components, can solve the problems of poor adhesion of photosensitive resist film, unrealizable wiring structure, and restricted wiring density, etc., to achieve excellent electrical performance, Small area occupation, simple and feasible process
- Summary
- Abstract
- Description
- Claims
- Application Information
AI Technical Summary
Problems solved by technology
Method used
Image
Examples
Embodiment Construction
[0025] Such as Figure 3~Figure 10 As shown, the present invention provides a method for forming a via hole in a printed circuit board, which mainly includes the following steps:
[0026] In the film sticking step, the double-sided copper-clad printed circuit board substrate (referred to as the substrate) that has been pre-drilled with via holes 10 by mechanical or laser means is pasted on the surface of the upper and lower copper layers 2 of the insulating dielectric layer 1 that need to be conductively connected. A photosensitive film 3 is attached, and a film opening 30 for limiting the electroplated copper area is formed on the photosensitive film 3 at a position corresponding to the via hole 10;
[0027] In the hole sealing electroplating step, on the first surface of the insulating dielectric layer 1, the film opening 30 formed in the film sticking step to limit the electroplating copper area is used, and the via hole 10 close to the first surface of the insulating diele...
PUM
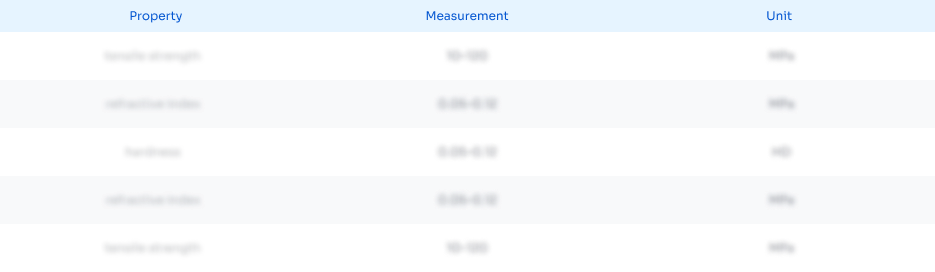
Abstract
Description
Claims
Application Information

- R&D Engineer
- R&D Manager
- IP Professional
- Industry Leading Data Capabilities
- Powerful AI technology
- Patent DNA Extraction
Browse by: Latest US Patents, China's latest patents, Technical Efficacy Thesaurus, Application Domain, Technology Topic, Popular Technical Reports.
© 2024 PatSnap. All rights reserved.Legal|Privacy policy|Modern Slavery Act Transparency Statement|Sitemap|About US| Contact US: help@patsnap.com