Numerical simulation technology for hollow section porthole die extrusion welding process
A technology for numerical simulation and hollow profiles, applied in metal extrusion dies, electrical digital data processing, special data processing applications, etc., can solve problems such as termination of simulation calculations
- Summary
- Abstract
- Description
- Claims
- Application Information
AI Technical Summary
Problems solved by technology
Method used
Image
Examples
Embodiment 1
[0045] By adopting the finite element simulation technology of the split die extrusion welding process of the present invention, the problem of mesh repair of the welding surface interpenetrating unit is solved, and the figure 1 The finite element simulation of the entire extrusion process of the square tube shown.
[0046] The size of the square tube is L30×t2mm, and the metal deformable body, that is, the blank diameter is Φ90mm, the extrusion cylinder diameter is Φ95mm, the extrusion ratio is 31.6, and the split ratio is 12.6. The shear friction model is selected between the blank and the mold, and the friction factor m=1 is selected according to the experimental results of ring compression.
[0047] The initial process conditions of the extrusion are: the temperature of the blank (A6005 aluminum alloy) is 480℃, the temperature of the extrusion cylinder is 400℃, the temperature of the die (H13 hot work die steel) is 450℃, the temperature of the extrusion pad is 30℃, and the extru...
Embodiment 2
[0064] The cross-section and dimensions of the asymmetric porous hollow profile are as Picture 20 As shown, the solid mold structure is as Figure 21 Shown. For this type of hollow section material with inconsistent welded surface and symmetry plane, only the welding surface mesh repair technology of the present invention can be used to complete the numerical simulation analysis of the entire extrusion process.
[0065] The finite element software Deform-3D is used for simulation, the mesh is divided by the absolute mesh method, the calculation unit is a tetrahedral mesh element, and the mesh element is refined at the entrance of the split hole and the entrance of the die hole with large plastic deformation. Set the minimum size of the unit during the simulation to 1mm and the maximum to 30mm.
[0066] Assuming that the diameter of the blank and the extrusion cylinder are both Φ238mm, the extrusion ratio is 31, a shear friction model is selected between the blank and the die, and ...
PUM
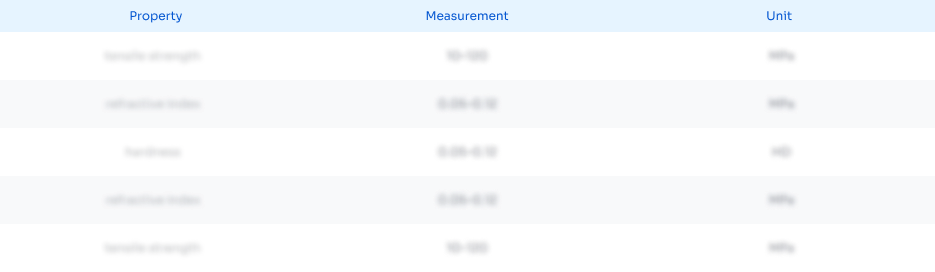
Abstract
Description
Claims
Application Information

- R&D
- Intellectual Property
- Life Sciences
- Materials
- Tech Scout
- Unparalleled Data Quality
- Higher Quality Content
- 60% Fewer Hallucinations
Browse by: Latest US Patents, China's latest patents, Technical Efficacy Thesaurus, Application Domain, Technology Topic, Popular Technical Reports.
© 2025 PatSnap. All rights reserved.Legal|Privacy policy|Modern Slavery Act Transparency Statement|Sitemap|About US| Contact US: help@patsnap.com