Method for directly deoxygenizing ferro-nickel in shaft furnace by using laterite nickel ore as raw material
A technology for laterite nickel ore and raw materials, which is applied in the field of metallurgical manufacturing, can solve the problems of low degree of automation, high carbon content in ferronickel, and high production cost, and achieves easy process control, low carbon content in ferronickel, and small investment. Effect
- Summary
- Abstract
- Description
- Claims
- Application Information
AI Technical Summary
Problems solved by technology
Method used
Examples
specific Embodiment approach 1
[0006] Specific embodiment one: the method described in this embodiment is realized in this way: select laterite nickel ore as raw material, the quality of nickel in the laterite nickel ore raw material accounts for 0.75%~2.60% of the total mass of laterite nickel ore, and the quality of iron accounts for 8.00% to 55.0% of the total mass of the laterite nickel ore; the laterite nickel ore and the reducing agent are loaded into the shaft furnace according to the weight ratio of 1.00:0.08 to 0.25, and then preheated and dried, heated and reduced, and released from the furnace. After crushing, ball milling, magnetic separation, and briquetting, qualified direct reduced ferronickel is obtained; the preheating and drying temperature is 700°C to 900°C, and the preheating and drying time is 2h to 4h; the heating reduction temperature is 900°C ~1300℃, heating reduction time is 4h~8h. In this embodiment, the reducing agent is coal powder or coke powder. The crushing, ball milling, mag...
specific Embodiment approach 2
[0007] Specific embodiment two: the difference between this embodiment and specific embodiment one is: the quality of nickel in the laterite nickel ore raw material described in this embodiment accounts for 0.75% to 1.49% of the total mass of laterite nickel ore, and the quality of iron accounts for 0.75% to 1.49% of the laterite nickel ore. 35.0% to 50.0% of the total mass of the ore (belonging to low nickel and high iron); the laterite nickel ore and reducing agent are loaded into the shaft furnace according to the ratio of 1:0.20 to 0.25 by weight, and the preheating and drying temperature is 800 ℃~900℃, the preheating and drying time is 3h~4h; the heating reduction temperature is 1000℃~1300℃, and the heating reduction time is 5h~8h. In the reduced ferronickel obtained in this embodiment, the mass of nickel accounts for 1.3% to 3.3% of the total mass of reduced ferronickel, and the mass of iron accounts for 70% to 95% of the total mass of reduced ferronickel.
specific Embodiment approach 3
[0008] Specific embodiment three: The difference between this embodiment and specific embodiment one is: the quality of nickel in the laterite nickel ore raw material described in this embodiment accounts for 1.50% to 2.60% of the total mass of laterite nickel ore, and the quality of iron accounts for 1.50% to 2.60% of the laterite nickel ore. 40.0% to 55.0% of the total mass of the ore (belonging to high nickel and high iron); the laterite nickel ore and reducing agent are loaded into the shaft furnace according to the ratio of 1:0.15 to 0.25 by weight, and the preheating and drying temperature is 700 ℃~800℃, the preheating and drying time is 2h~3h; the heating reduction temperature is 900℃~1200℃, and the heating reduction time is 4h~7h. In the reduced ferronickel obtained in this embodiment, the mass of nickel accounts for 2.5%-5.5% of the total mass of reduced ferronickel, and the mass of iron accounts for 75%-95% of the total mass of reduced ferronickel.
PUM
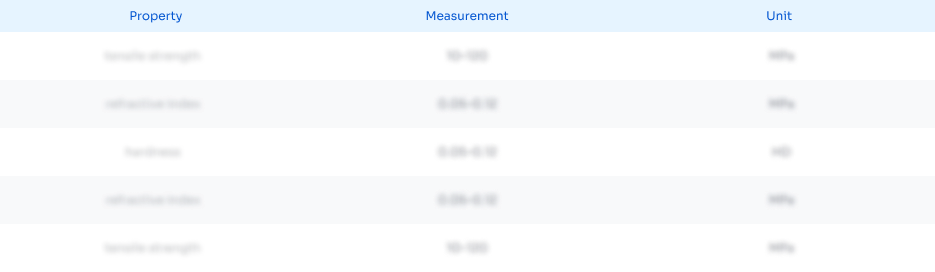
Abstract
Description
Claims
Application Information

- R&D Engineer
- R&D Manager
- IP Professional
- Industry Leading Data Capabilities
- Powerful AI technology
- Patent DNA Extraction
Browse by: Latest US Patents, China's latest patents, Technical Efficacy Thesaurus, Application Domain, Technology Topic, Popular Technical Reports.
© 2024 PatSnap. All rights reserved.Legal|Privacy policy|Modern Slavery Act Transparency Statement|Sitemap|About US| Contact US: help@patsnap.com