Production technology of embossing laminating release paper
A technology of embossed film release and production technology, which is applied in lamination, paper, papermaking, etc., can solve the problems of inconvenient cutting, uneven distribution of lines, and many waste materials, and achieve good publicity effects, uniform distribution lines, and The effect of unity of depth and light
- Summary
- Abstract
- Description
- Claims
- Application Information
AI Technical Summary
Problems solved by technology
Method used
Examples
Embodiment Construction
[0011] A kind of manufacture technology of embossed coating release paper, it is characterized in that comprising the following steps:
[0012] 1) Preparation of laminating coating
[0013] Put the high-density polyethylene and low-density polyethylene into the mixing container according to the weight ratio of 1:1.5-2, mix and stir for 5-10 minutes to make the two evenly mixed, and extrude the feeding screw in the system through the laminating machine Heating and bridging at 180-245°C to melt the polyethylene mixture to achieve sufficient bridging to facilitate the strengthening of molecular chain links, and then further heating the polyethylene mixture to 310-360°C on the feed screw to make it a molten fluid Shape and pressurize to 5Mpa-20Mpa at the same time, when the polyethylene mixture passes through the outlet of the screw, a die head heats the polyethylene mixture at 320-360°C, and turns it into a cloth shape and extrudes it.
[0014] 2) Preparation of embossed film re...
PUM
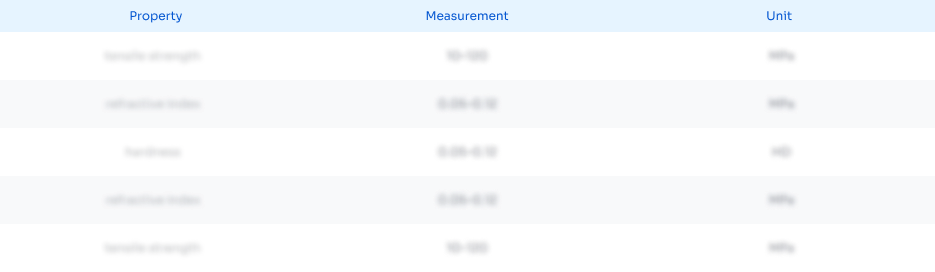
Abstract
Description
Claims
Application Information

- R&D
- Intellectual Property
- Life Sciences
- Materials
- Tech Scout
- Unparalleled Data Quality
- Higher Quality Content
- 60% Fewer Hallucinations
Browse by: Latest US Patents, China's latest patents, Technical Efficacy Thesaurus, Application Domain, Technology Topic, Popular Technical Reports.
© 2025 PatSnap. All rights reserved.Legal|Privacy policy|Modern Slavery Act Transparency Statement|Sitemap|About US| Contact US: help@patsnap.com