Preparation method of filled-type thermally conductive silicone rubber composite material
A technology of thermally conductive silicone rubber and composite materials, applied in the field of preparation of high thermal conductivity composite materials, can solve the problems of poor component effect, large thermal expansion coefficient, small thermal conductivity, etc., to prevent moisture, small thermal expansion coefficient, and improve thermal conductivity. Effect
- Summary
- Abstract
- Description
- Claims
- Application Information
AI Technical Summary
Problems solved by technology
Method used
Examples
Embodiment 1
[0026] (1) Mix and stir 50 parts by mass of carbon-coated copper nanoparticles with 95% ethanol solution, dry at 120° C. for 10 hours, and then dry at 150° C. for 1 hour, and put them into a desiccator for use.
[0027] (2) Add 100 parts by mass of silicone rubber raw rubber to the roller, after the raw rubber wraps the roller, then add 50 parts by mass of thermally conductive filler and 1-3 parts by mass of hydroxyl silicone oil. Repeatedly knead on the roller for about 40 minutes until uniform, thin pass 5-10 times. Add 2.5 parts by mass of vulcanizing agent Shuang25, knead evenly, and thinly pass the lower sheet to obtain the silicone rubber compound.
[0028] (3) Put the mixed silicone rubber into the mold, and after filling the mold with cold pressure, place the mold on a flat vulcanizing machine for one-stage vulcanization. Under the condition of 5min-10min, vulcanization molding is adopted by molding method, and a sample with uniform thickness is pressed;
[0029] (4)...
Embodiment 2
[0032] (1) Mix and stir 100 parts by mass of carbon-coated copper nanoparticles with 95% ethanol solution, dry at 120° C. for 10 h, and then dry at 150° C. for 1 h, and put it into a desiccator for use.
[0033] (2) Add 100 parts by mass of silicone rubber raw rubber to the roller, after the raw rubber wraps the roller, then add 100 parts by mass of thermally conductive filler and 1.5 parts by mass of hydroxyl silicone oil. Repeatedly knead on the roller until uniform, thin pass 5-10 times. Add 2.5 parts by mass of vulcanizing agent Shuang25, knead evenly, and thinly pass the lower sheet to obtain the silicone rubber compound.
[0034](3) Put the mixed silicone rubber into the mold, and after filling the mold with cold pressure, place the mold on a flat vulcanizing machine for one-stage vulcanization. Under the condition of 5min-10min, vulcanization molding is adopted by molding method, and a sample with uniform thickness is pressed;
[0035] (4) The sample after the first-s...
Embodiment 3
[0038] (1) Mix and stir 150 parts by mass of carbon-coated copper nanoparticles with 95% ethanol solution, dry at 120° C. for 10 hours, and then dry at 150° C. for 1 hour, and put it into a desiccator for use.
[0039] (2) Add 100 parts by mass of silicone rubber raw rubber to the roller, after the raw rubber wraps the roller, then add 150 parts by mass of thermally conductive filler and 1-3 parts by mass of hydroxyl silicone oil. Repeatedly knead on the roller until uniform, thin pass 5-10 times. Add 2.5 parts by mass of vulcanizing agent Shuang25, knead evenly, and thinly pass the lower sheet to obtain the silicone rubber compound.
[0040] (3) Put the mixed silicone rubber into the mold, and after filling the mold with cold pressure, place the mold on a flat vulcanizing machine for one-stage vulcanization. Under the condition of 5min-10min, vulcanization molding is adopted by molding method, and a sample with uniform thickness is pressed;
[0041] (4) The sample after the...
PUM
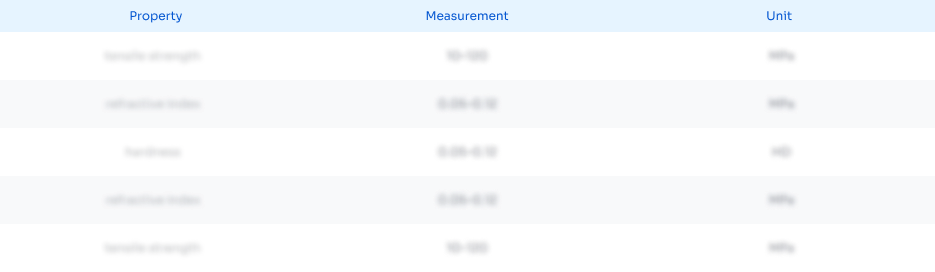
Abstract
Description
Claims
Application Information

- R&D
- Intellectual Property
- Life Sciences
- Materials
- Tech Scout
- Unparalleled Data Quality
- Higher Quality Content
- 60% Fewer Hallucinations
Browse by: Latest US Patents, China's latest patents, Technical Efficacy Thesaurus, Application Domain, Technology Topic, Popular Technical Reports.
© 2025 PatSnap. All rights reserved.Legal|Privacy policy|Modern Slavery Act Transparency Statement|Sitemap|About US| Contact US: help@patsnap.com