Method of comprehensively use of chloronitrobenzene mixture by fluoro-reaction
A technology of monochloronitrobenzene and chloronitrobenzene, which is applied in the field of comprehensive utilization of o-, m-, and p-chloronitrobenzene mixtures, can solve the problems of many steps and poor utilization of resources, and achieve simple operation Effect
- Summary
- Abstract
- Description
- Claims
- Application Information
AI Technical Summary
Problems solved by technology
Method used
Examples
Embodiment 1
[0019] Add 158 grams (1 mole) of a chloronitrobenzene mixture, 15.8 grams of catalyst tetrabutylammonium bromide, and 157 grams (2.7 moles) of anhydrous potassium fluoride into the reaction flask, heat to 200 ° C, react for 5 hours, and filter Solids such as potassium chloride were removed, and 63.5 grams of p-fluoronitrobenzene and 12.7 grams of o-fluoronitrobenzene were separated through rectification in a rectification tower, with a total yield of 90%. The residue was recrystallized from toluene to obtain 60 g of m-chloronitrobenzene with a recovery rate of 95% and a purity of ≥99.5%.
Embodiment 2
[0021] Add 158 grams (1 mole) of a chloronitrobenzene mixture, 1.58 grams of catalyst tetrabutylammonium bromide, and 157 grams (2.7 moles) of anhydrous potassium fluoride into the reaction flask, heat to 150 ° C, react for 15 hours, and filter Solids such as potassium chloride were removed, and 65 grams of p-fluoronitrobenzene and 13 grams of o-fluoronitrobenzene were separated through rectification in a rectification tower, with a total yield of 92%. The residue was recrystallized from toluene to obtain 60 g of m-chloronitrobenzene with a recovery rate of 95% and a purity of ≥99.5%.
Embodiment 3
[0023] Add 158 grams (1 mole) of a chloronitrobenzene mixture, 158 grams of catalyst calix[6]arene, and 476 grams (8.2 moles) of anhydrous potassium fluoride into the reaction flask, heat to 150°C, react for 5 hours, and remove by filtration Potassium chloride and other solids were rectified by a rectification tower to separate 67 grams of p-fluoronitrobenzene and 13.4 grams of o-fluoronitrobenzene, with a total yield of 95%. The residue was recrystallized from toluene to obtain 60 g of m-chloronitrobenzene with a recovery rate of 95% and a purity of ≥99.5%.
PUM
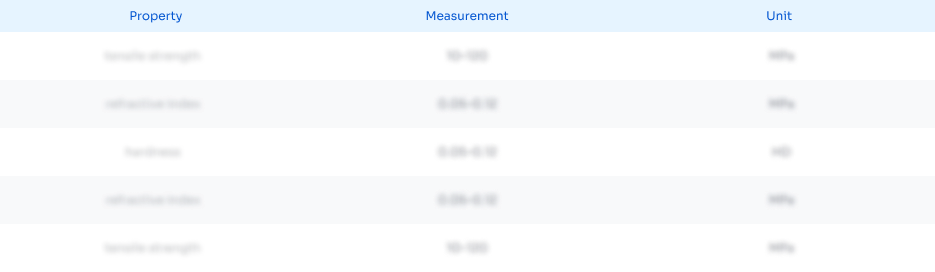
Abstract
Description
Claims
Application Information

- Generate Ideas
- Intellectual Property
- Life Sciences
- Materials
- Tech Scout
- Unparalleled Data Quality
- Higher Quality Content
- 60% Fewer Hallucinations
Browse by: Latest US Patents, China's latest patents, Technical Efficacy Thesaurus, Application Domain, Technology Topic, Popular Technical Reports.
© 2025 PatSnap. All rights reserved.Legal|Privacy policy|Modern Slavery Act Transparency Statement|Sitemap|About US| Contact US: help@patsnap.com