Regeneration method for removing catalyst carbon deposit
A technology for catalyst and coke deposition, which is applied in catalyst regeneration/reactivation, chemical instruments and methods, physical/chemical process catalysts, etc. It can solve the problems of complex cleaning agent composition, complicated operation, phenol toxicity, etc., and achieve easy implementation and operation. The effect of low temperature and short operation process
- Summary
- Abstract
- Description
- Claims
- Application Information
AI Technical Summary
Problems solved by technology
Method used
Image
Examples
Embodiment 1
[0025] The Na-K-Mg / HZSM-5 catalyst deactivated by carbon deposits was taken out from the reaction tube, and dried in an oven for 1.5 hours at a temperature of 105 degrees Celsius. The dried catalyst was taken out and weighed to obtain 0.65 g.
[0026] Soak the dried catalyst with methanol at 20° C. for 5 hours, and the volume of methanol used is 1.5 times the volume of the catalyst. Filter out the catalyst, put it in a muffle furnace and dry it at a constant temperature of 100°C for 3 hours, then raise the temperature of the muffle furnace to 200°C for calcination at a constant temperature for 4 hours, and finally raise the temperature of the muffle furnace to 400°C for 4 hours. Take out and weigh 0.59g. The catalyst weight decreased by 9.2% after regeneration, indicating that the carbon deposits were removed.
[0027] The catalyst is loaded into the HL-1A multifunctional micro-high pressure reaction system manufactured by Hangzhou Huali Pump Industry Co., Ltd. to catalyze th...
Embodiment 2
[0032] The carbon-deactivated Ni-Co-Mn / SAPO-34 catalyst was taken out from the reaction tube and dried in an oven for 1.5 hours at a temperature of 105 degrees Celsius. The dried catalyst was taken out and weighed to obtain 0.64 g.
[0033] Soak the dried catalyst with methanol at 30° C. for 4 hours, and the volume of methanol used is twice the volume of the catalyst. Filter out the catalyst, put it in a muffle furnace and dry it at a constant temperature of 110°C for 2.5 hours, then raise the temperature of the muffle furnace to 250°C for 3 hours, and finally raise the temperature of the muffle furnace to 450°C for 3 hours. Take out and weigh 0.57g. The catalyst weight decreased by 10.9% after regeneration, indicating that the carbon deposits were removed.
[0034] The catalyst is loaded into the HL-1A multifunctional micro-high pressure reaction system manufactured by Hangzhou Huali Pump Industry Co., Ltd. to catalyze the reaction of methanol to light olefins. The reaction ...
Embodiment 3
[0039] The Na-K / HZSM-5 catalyst that the coking deactivation is taken out from the reaction tube is dried in an oven for 1.5 hours, and the drying temperature is 105 degrees Celsius. The dried catalyst is taken out and weighed to obtain 0.64g.
[0040] Soak the dried catalyst with methanol at 40° C. for 3 hours, and the volume of methanol used is 2.5 times the volume of the catalyst. Filter out the catalyst, put it into a muffle furnace and dry it at a constant temperature of 120°C for 2 hours, then raise the temperature of the muffle furnace to 300°C for 2 hours, and finally raise the temperature of the muffle furnace to 500°C for 2 hours. Take out and weigh 0.58g. The catalyst weight decreased by 9.3% after regeneration, indicating that the carbon deposits were removed.
[0041] The catalyst is loaded into the HL-1A multifunctional micro-high pressure reaction system manufactured by Hangzhou Huali Pump Industry Co., Ltd. to catalyze the reaction of methanol to light olefins...
PUM
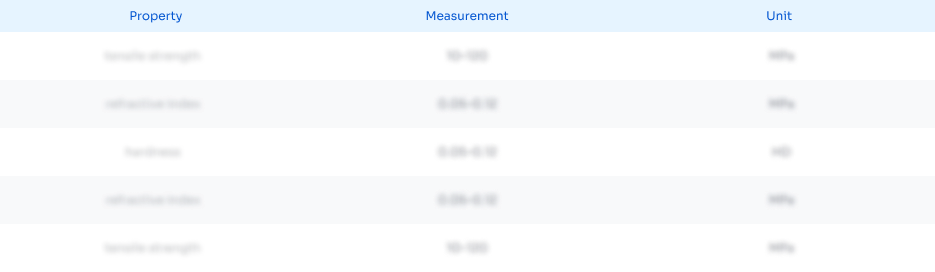
Abstract
Description
Claims
Application Information

- Generate Ideas
- Intellectual Property
- Life Sciences
- Materials
- Tech Scout
- Unparalleled Data Quality
- Higher Quality Content
- 60% Fewer Hallucinations
Browse by: Latest US Patents, China's latest patents, Technical Efficacy Thesaurus, Application Domain, Technology Topic, Popular Technical Reports.
© 2025 PatSnap. All rights reserved.Legal|Privacy policy|Modern Slavery Act Transparency Statement|Sitemap|About US| Contact US: help@patsnap.com