Hot-compress dip-coating insulation method of copper bar
A technology of hot compress and dip coating, which is applied in the field of copper bar insulation and copper bar hot dip coating insulation, which can solve the problems of high labor intensity and unguaranteed quality of copper bar insulation, and achieve labor intensity reduction, stable and reliable product quality, and high production efficiency. high effect
- Summary
- Abstract
- Description
- Claims
- Application Information
AI Technical Summary
Problems solved by technology
Method used
Image
Examples
Embodiment Construction
[0012] Copper row hot-coating dip-coating insulation method, the method is realized by the following steps: a. Clean the copper row, and then protect and wrap the electrical contact surface of the copper row; b. Put the copper row at a temperature of 170 ° C (or 175 ℃, or 178°C, or 182°C, or 188°C, or 190°C) and keep warm at this temperature for 20 minutes; c. Fluidize the preheated copper row in the epoxy encapsulation material In the bed, heat the surface of the copper bar with epoxy encapsulation material, and then quickly shake the floating powder on the surface of the copper bar; d, remove the protection of the electrical contact surface of the copper bar after the hot compress and trim the end; e, the copper bar at a temperature of Cured at 140°C (or 142°C, or 145°C, or 148°C, or 149°C, or 150°C) for 30 minutes and then dried naturally. When the copper bar is preheated, the copper bar with a thickness of less than 5mm is preheated at a temperature of 170°C (or 172°C, or ...
PUM
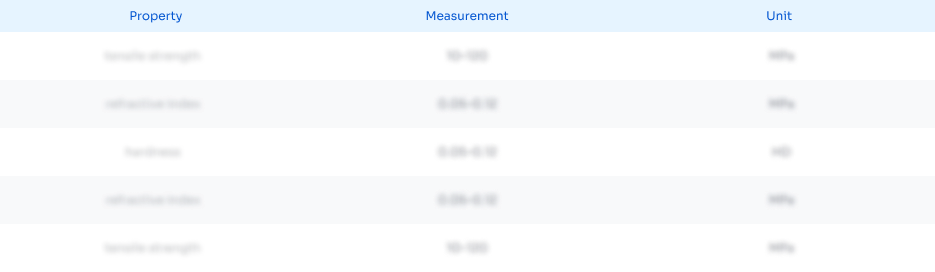
Abstract
Description
Claims
Application Information

- R&D
- Intellectual Property
- Life Sciences
- Materials
- Tech Scout
- Unparalleled Data Quality
- Higher Quality Content
- 60% Fewer Hallucinations
Browse by: Latest US Patents, China's latest patents, Technical Efficacy Thesaurus, Application Domain, Technology Topic, Popular Technical Reports.
© 2025 PatSnap. All rights reserved.Legal|Privacy policy|Modern Slavery Act Transparency Statement|Sitemap|About US| Contact US: help@patsnap.com