Method for manufacturing intelligent composite-material laminates used for monitoring structural longitudinal strain
A composite material layer and manufacturing method technology, applied in measurement devices, optical devices, instruments, etc., can solve the problems affecting the grating strain measurement accuracy, the process cannot be guaranteed, and the optical fiber is easily damaged, so as to improve the strain monitoring accuracy and avoid chirps. Chirp phenomenon, the effect that meets the sensitivity requirements
- Summary
- Abstract
- Description
- Claims
- Application Information
AI Technical Summary
Problems solved by technology
Method used
Image
Examples
Embodiment Construction
[0016] see figure 1 , a method for manufacturing an intelligent composite laminate for structural longitudinal strain monitoring, the steps are as follows:
[0017] (1) Choose a CFRP with a thickness of 0.2mm or a GFRP composite prepreg with a thickness of 0.15mm. CFRP is laminated according to the warp / weft direction of 50 / 50 (mass ratio); GFRP is laid according to the warp / weft direction of 80 / 20 (mass ratio) ) of the lay-up structure lay-up;
[0018] (2) The composite material prepreg is cut according to 100mm×20mm, and the layers are laid by hand;
[0019] (3) Apply prestress at both ends of the fiber grating to be embedded, put it into the composite material laminate along the 100mm direction, and embed the port part into the composite material with a quartz protective sleeve;
[0020] (4) Seal the composite material layer with a vacuum bag, and the fiber grating passes through the vacuum bag through the silicone rubber sealing strip;
[0021] (5) Put the composite lay...
PUM
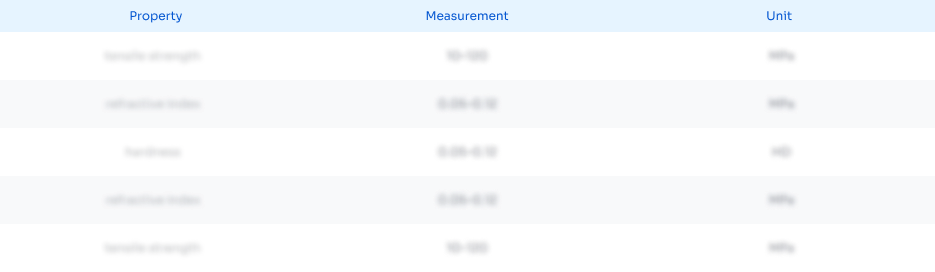
Abstract
Description
Claims
Application Information

- Generate Ideas
- Intellectual Property
- Life Sciences
- Materials
- Tech Scout
- Unparalleled Data Quality
- Higher Quality Content
- 60% Fewer Hallucinations
Browse by: Latest US Patents, China's latest patents, Technical Efficacy Thesaurus, Application Domain, Technology Topic, Popular Technical Reports.
© 2025 PatSnap. All rights reserved.Legal|Privacy policy|Modern Slavery Act Transparency Statement|Sitemap|About US| Contact US: help@patsnap.com