Fiber reinforced rubber
A fiber reinforced and rubber technology, applied in the field of fiber reinforced rubber, can solve the problems that the strength and deformation resistance of rubber cannot meet the requirements of use, the effect is not very ideal, and the fibers cannot be dispersed evenly, etc., to increase the tear resistance and excellent physical properties. Mechanical properties, the effect of good elasticity
- Summary
- Abstract
- Description
- Claims
- Application Information
AI Technical Summary
Problems solved by technology
Method used
Image
Examples
Embodiment 1-9
[0023] The ratio of raw materials by weight is shown in Table 1. The preparation process is as follows:
[0024] (1) Mix polypropylene fiber, glass fiber, white carbon black and activated calcium carbonate together at high speed in a container to make a pre-dispersion of uniformly dispersed short fiber and powder.
[0025] (2) Put styrene-butadiene rubber and high styrene resin into the closed rubber mixer for plasticizing and kneading. The plasticizing time is 5-6 minutes, and the plasticizing temperature is controlled at 120-130°C. Mixing agent, anti-aging agent, colorant and pre-dispersion, the mixing time is not less than 15min, and the mixing temperature is controlled below 130°C.
[0026] (3) After mixing, discharge the material to the open rubber mixer and add vulcanizing agent. When adding vulcanizing agent, the roller temperature should be controlled below 100°C to avoid scorching. Then unload the sheet to cool and park; during this period, a quick inspection of the...
Embodiment 10-18
[0031] The ratio of raw materials by weight is shown in Table 2.
[0032] Table 2 The ratio of raw materials used in Examples 10-18
[0033]
[0034] The preparation process is as follows:
[0035] (1) Aramid fiber, glass fiber, white carbon black and activated calcium carbonate are stirred together at high speed in a container to make a pre-dispersion of short fiber and reinforcing filler with uniform dispersion.
[0036] (2) Nitrile rubber is subjected to low-temperature first and second-stage low-temperature thin-pass masticating on an open rubber mixer. The roller temperature is controlled at 50±5°C. The first-stage masticating roller distance is 1-2 mm, and the number of roll passes is 25 times. ;After parking for 8 hours, carry out the second stage of mastication, the roller distance is 1-2mm, and the number of roller passes is 20 times. Weigh and park for use. Refining is invalid. Then put the masticated nitrile rubber and chlorinated polyethylene resin into the c...
Embodiment example 19-21
[0040] The ratio of raw materials by weight is shown in Table 3. The preparation process is as follows:
[0041] (1) Mix glass fiber, carbon fiber and high wear-resistant furnace carbon black together at high speed in a container to make a pre-dispersion with uniform dispersion.
[0042](2) Plasticize the chloroprene rubber 20 times on the open rubber mixer, control the roller temperature at 50±5°C, put the chloroprene rubber into the internal mixer after plastication, and add the active agent, fiber Mix with the pre-dispersion of reinforcing agent, the mixing time is not less than 15min, and the mixing temperature is controlled below 130°C.
[0043] (3) After mixing evenly, discharge the material to the open mill to add vulcanizing agent. When adding vulcanizing agent, the roller temperature should be controlled below 100°C to avoid scorching. Then unload the sheet and park it for cooling. During this period, a quick inspection of the physical and mechanical properties is c...
PUM
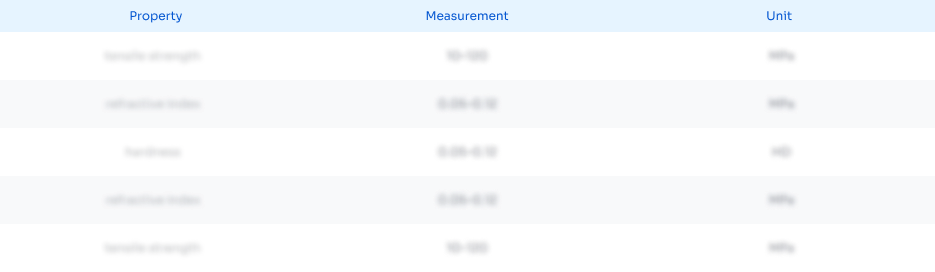
Abstract
Description
Claims
Application Information

- R&D
- Intellectual Property
- Life Sciences
- Materials
- Tech Scout
- Unparalleled Data Quality
- Higher Quality Content
- 60% Fewer Hallucinations
Browse by: Latest US Patents, China's latest patents, Technical Efficacy Thesaurus, Application Domain, Technology Topic, Popular Technical Reports.
© 2025 PatSnap. All rights reserved.Legal|Privacy policy|Modern Slavery Act Transparency Statement|Sitemap|About US| Contact US: help@patsnap.com