Angle parametrized macro modelling method of micro-electro-mechanism system
A technology of micro-electromechanical systems and angle parameters, applied in chemical instruments and methods, electrical digital data processing, circuits, etc.
- Summary
- Abstract
- Description
- Claims
- Application Information
AI Technical Summary
Problems solved by technology
Method used
Image
Examples
Embodiment Construction
[0029] The present invention will be further described below in conjunction with a macro-modeling process of a plane accelerometer's folded beam angle parameterization. Refer to attached image 3 , the frame structure of the accelerometer is composed of folded beam 1 in the upper left corner, folded beam 2 in the upper right corner, folded beam 3 in the lower left corner, folded beam 4 in the lower right corner and mass block 5, which is symmetrical about the origin o center of the coordinate system oxyz and x, y The axis symmetry of the coordinate axis, there is a folded beam with complex structure on the upper left, upper right, lower left, and lower right of the accelerometer. The specific steps of the angle parametric macro modeling process of the folded beam are as follows:
[0030] Step 1: Select the folded beam 1 in the upper left corner as the reference structure, use the finite element software ANSYS, and select the beam188 unit for modal analysis. The finite element...
PUM
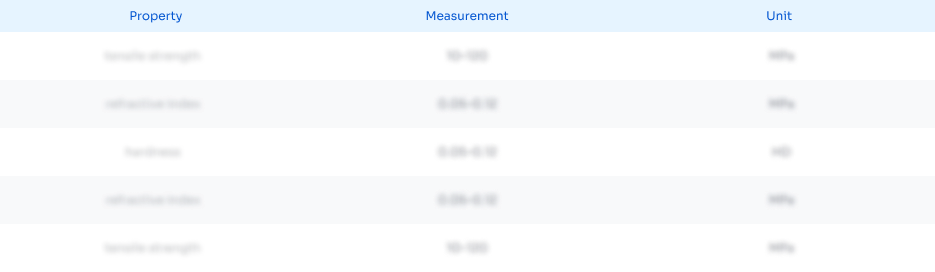
Abstract
Description
Claims
Application Information

- R&D
- Intellectual Property
- Life Sciences
- Materials
- Tech Scout
- Unparalleled Data Quality
- Higher Quality Content
- 60% Fewer Hallucinations
Browse by: Latest US Patents, China's latest patents, Technical Efficacy Thesaurus, Application Domain, Technology Topic, Popular Technical Reports.
© 2025 PatSnap. All rights reserved.Legal|Privacy policy|Modern Slavery Act Transparency Statement|Sitemap|About US| Contact US: help@patsnap.com