Rolling method for improving outer layer thickness distribution of composite plate
A technology of thickness distribution and clad plate, applied in the direction of metal rolling, metal rolling, rolling mill control device, etc., can solve the problems of material waste, increase the amount of plate edge reduction, affect the brazability of clad aluminum foil, etc.
- Summary
- Abstract
- Description
- Claims
- Application Information
AI Technical Summary
Problems solved by technology
Method used
Image
Examples
Embodiment 1
[0034] Example 1: The rolling process of a three-layer composite aluminum plate in a factory: mainly for preparing ingot casting-welding and compounding-heating-hot rolling-cold rolling-finishing-packaging.
[0035] The specific process of hot rolling in the hot rolling stage of the three-layer composite plate is that the cleaned core layer and cladding layer are welded and compounded, and the compounded material can be rolled after being heated in a heating furnace. Combined with the actual production conditions of the factory, a two-roll reversing rolling mill with constant speed, same direction and equal diameter is used for reciprocating rolling. The diameter of the working roll is 500mm, the rolling speed is 1.5m / s, and the starting and finishing temperatures are 500°C respectively. , 400°C. The process parameters of the main rolling passes are shown in the table below:
[0036] The original process parameters of a factory
[0037]
[0038] Process parameters provide...
PUM
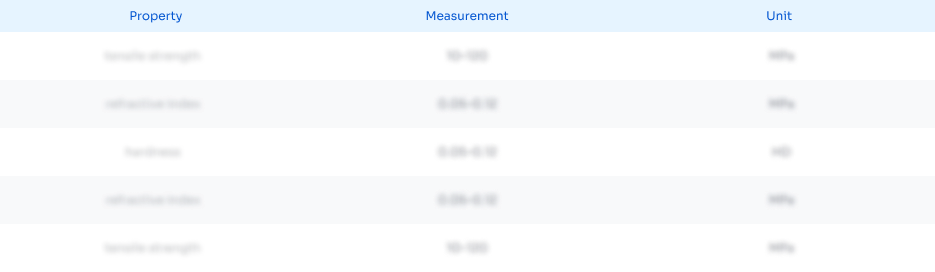
Abstract
Description
Claims
Application Information

- R&D
- Intellectual Property
- Life Sciences
- Materials
- Tech Scout
- Unparalleled Data Quality
- Higher Quality Content
- 60% Fewer Hallucinations
Browse by: Latest US Patents, China's latest patents, Technical Efficacy Thesaurus, Application Domain, Technology Topic, Popular Technical Reports.
© 2025 PatSnap. All rights reserved.Legal|Privacy policy|Modern Slavery Act Transparency Statement|Sitemap|About US| Contact US: help@patsnap.com