Preparation method for biodegradable fluorescent polyester multipolymer
A biodegradable and copolymer technology, applied in the field of functional materials, can solve the problem of increasing white blood cells
- Summary
- Abstract
- Description
- Claims
- Application Information
AI Technical Summary
Problems solved by technology
Method used
Image
Examples
Embodiment 1
[0030] Weigh 1.8012g (10mmol) of 3,4-dihydroxycinnamic acid (DHCA), 0.3215g (0.8mmol) of polyethylene glycol 400 (PEG400), 0.0085g (0.1mmol) of sodium acetate (ACONa), and measure acetic anhydride (AC 2 O) 10mL, put it into a 100mL three-necked flask, raise the temperature of the three-necked flask to 110°C at a stirring speed of 200r / min, heat up to 190°C after 1.5h of reaction, reduce the stirring speed to 120r / min and then react at a constant temperature for 7h, the whole reaction process in N 2 Protected and protected from light.
[0031] Wash twice with deionized water, then wash twice with absolute ethanol, remove unreacted monomers and catalysts, and then dry naturally to obtain a yellow or light yellow powder product.
Embodiment 2
[0033] Weigh 1.8026g (10mmol) of 3,4-dihydroxycinnamic acid (DHCA), 0.3863g (4.3mmol) of lactic acid (D, L-LA), 0.0310g (0.4mmol) of sodium acetate (ACONa), and measure acetic anhydride (AC 2 (2) 20mL, add in 250mL there-necked flask, the temperature of the three-necked flask is raised to 120°C at a stirring speed of 360r / min, the temperature is raised to 210°C after 2h of reaction, the stirring speed is reduced to 150r / min and then reacted at a constant temperature for 6h, the whole reaction process is at N 2 Protected and protected from light.
[0034] Wash twice with deionized water, then wash twice with absolute ethanol, remove unreacted monomers and catalysts, and then dry naturally to obtain a yellow or light yellow powder product.
Embodiment 3
[0036] Take by weighing 3.6042g (20mmol) of 3,4-dihydroxycinnamic acid (DHCA), 0.6909g (5.0mmol) of p-hydroxybenzoic acid (p-HA), 0.0167g (0.2mmol) of sodium acetate (ACONa), and measure B Anhydride (AC 2 (0) 18mL, add in 250mL there-necked flask, the temperature of the three-necked flask is raised to 135°C at a stirring speed of 400r / min, the temperature is raised to 210°C after 2 hours of reaction, the stirring speed is reduced to 130r / min and then reacted at constant temperature for 9h, the whole reaction process is in N 2 Protected and protected from light.
[0037] Wash twice with deionized water, then wash twice with absolute ethanol, remove unreacted monomers and catalysts, and then dry naturally to obtain a yellow or light yellow powder product.
PUM
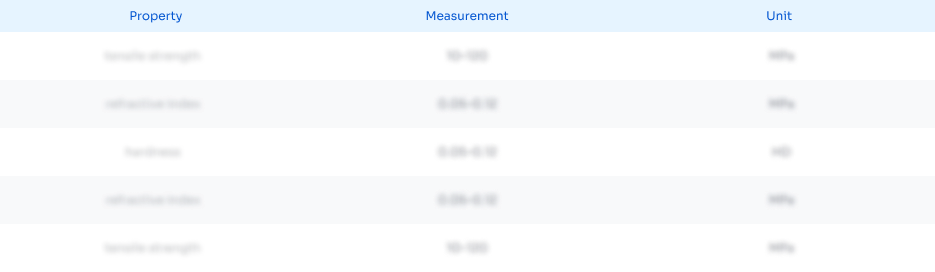
Abstract
Description
Claims
Application Information

- R&D Engineer
- R&D Manager
- IP Professional
- Industry Leading Data Capabilities
- Powerful AI technology
- Patent DNA Extraction
Browse by: Latest US Patents, China's latest patents, Technical Efficacy Thesaurus, Application Domain, Technology Topic, Popular Technical Reports.
© 2024 PatSnap. All rights reserved.Legal|Privacy policy|Modern Slavery Act Transparency Statement|Sitemap|About US| Contact US: help@patsnap.com