Sludge stirring system
A stirring system and sludge technology, applied in the direction of dewatering/drying/concentrating sludge treatment, etc., can solve the problems of poor dehydration effect, large additives, inability to disperse sewage and sludge to mix evenly, etc.
- Summary
- Abstract
- Description
- Claims
- Application Information
AI Technical Summary
Problems solved by technology
Method used
Image
Examples
Embodiment 1
[0030] Such as figure 1 As shown, the sludge mixing system includes a cylindrical mixing tank 1, a tank cover 2 installed on the mixing tank 1, a sludge inlet 3 provided on the tank cover 2, and a side wall of the mixing tank 1 close to the The sludge outlet 4 at the bottom of the stirring tank 1, the driving device 5 installed on the tank cover 2, the stirring shaft 6 coaxially installed with the driving device 5, fixed on the stirring shaft 6 with the stirring shaft 6 as the center of symmetry and The vertical blade shaft 7 of the stirring shaft 6, the stirring blade 8 fixed on the blade shaft 7, the baffle plate 9 installed on the inner side wall of the stirring tank 1 above its corresponding stirring blade 8, the baffle plate 9 fixed on the bottom of the stirring tank 1 bracket12.
[0031] The mixing tank 1 is made of stainless steel, with an outer diameter of 4 meters and a height of 5 meters. The stirring tank 1 and the tank cover 2 form a closed inner cavity.
[0032...
Embodiment 2
[0034] Such as figure 2 As shown, the difference from Embodiment 1 is that the stirring tank 21 is made of aluminum alloy, with an outer diameter of 1 meter and a height of 1.5 meters. The stirring blades 22 are a group, and the radial distance between the outer diameter of the blade shaft 26 and the inner wall of the stirring tank 21 is 0.08 meters. A positioning protrusion 23 is protruded from the bottom of the stirring tank 21 , and a positioning recess 24 cooperating with the positioning protrusion 23 is provided at the end of the stirring shaft.
[0035] The number of each group of baffles 25 is 2, and the vertical spacing of the corresponding stirring blades 22 is 0.3 meters; the angle at which the baffles 25 are installed is 40° with the horizontal plane; The arc surface of the stirring tank 21 is changed to an arc shape, the maximum radial width is 0.1 meters, and the length is 0.15 meters.
Embodiment 3
[0037] Such as image 3 As shown, the difference from Example 1 is that the stirring tank 31 is made of glass fiber reinforced plastic, with an outer diameter of 3 meters, a height of 4.3 meters, and a wall thickness of 3 centimeters.
[0038] The stirring blades 32 are a group, and the radial distance between the outer diameter of the blade shaft 38 and the inner wall of the stirring tank 31 is 0.1 meter.
[0039] The baffle 33 is L-shaped, and the vertical distance between the corresponding stirring blades 32 is 1.1 meters. The angle that the long arm 36 of baffle 33 is installed is counterclockwise with the direction of rotation of stirring blade 32, and becomes 45 ° with horizontal plane; The long arm 36 of baffle 32 is rectangular, wide 0.2 meter, long 0.3 meter.
[0040] The bottom of the stirring tank is not provided with a fixed support, but a stirring tank chassis 37 is provided, and fine sand (not shown) is housed in the stirring tank chassis 37, and the stirring ta...
PUM
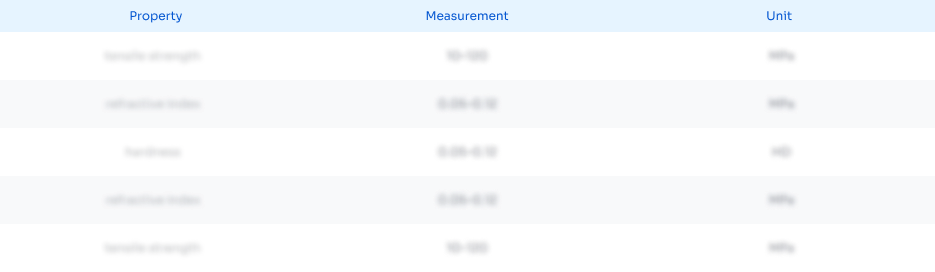
Abstract
Description
Claims
Application Information

- R&D
- Intellectual Property
- Life Sciences
- Materials
- Tech Scout
- Unparalleled Data Quality
- Higher Quality Content
- 60% Fewer Hallucinations
Browse by: Latest US Patents, China's latest patents, Technical Efficacy Thesaurus, Application Domain, Technology Topic, Popular Technical Reports.
© 2025 PatSnap. All rights reserved.Legal|Privacy policy|Modern Slavery Act Transparency Statement|Sitemap|About US| Contact US: help@patsnap.com