Method for preparing silicon tetrafluoride
A silicon tetrafluoride and powder technology, which is applied in the production field of silicon tetrafluoride, can solve the problems of high purchasing cost of fluorite and rising cost of silicon tetrafluoride, and achieve the effect of reducing production cost.
- Summary
- Abstract
- Description
- Claims
- Application Information
AI Technical Summary
Problems solved by technology
Method used
Image
Examples
preparation example Construction
[0037] During the preparation of silane, a large amount of by-product NaAlF is produced 4 , in order to effectively resolve the by-product NaAlF 4 and reduce the production cost of silicon tetrafluoride, the present invention will include by-product NaAlF 4 The raw material, Si source and sulfuric acid are reacted to obtain silicon tetrafluoride. For NaAlF 4 , can also be prepared by other methods, and the present invention is not particularly limited.
[0038] In addition, it can also be found in the by-product NaAlF 4 Mix other F-containing materials in the mixture as raw materials for preparing silicon tetrafluoride, and other F-containing raw materials can be one or more of calcium fluoride, sodium fluoride, and sodium silicofluoride.
[0039] Select NaAlF 4 powder as a raw material, in order to facilitate the reaction, the preferred particle size is 50 mesh to 300 mesh NaAlF 4 Powder as raw material, more preferably, NaAlF 4 The particle size of the powder is prefe...
Embodiment 1
[0065] Dilute sodium aluminum hydride with dimethyl ether to a concentration of about 10%, then react with silicon tetrafluoride at a temperature of 50°C and a pressure of 0.1MPa, and collect the by-product NaAlF 4 , after drying, measure the collected NaAlF 4 The purity of 96.2% by weight, then the NaAlF 4 Grind until the particle size is 100 mesh to 150 mesh and set aside.
[0066] Weigh NaAlF 4 2.52 kg and 1.2 kg of silica powder with a particle size of 100 mesh to 150 mesh and a purity of 98% by weight are sent to a mixer and mixed, and stirred evenly;
[0067] The mixture obtained after mixing is sent to a calciner for a calcining reaction to form a complex, the calcining temperature is 300°C, and the calcining time is 20 minutes;
[0068] Load the calcined product into the reaction furnace (full volume is 0.08m 3 ), and then adding 3.92kg of concentrated sulfuric acid with a concentration of 98% by weight to react with the calcined product, the temperature of the rea...
Embodiment 2
[0070] Get the NaAlF that embodiment 1 prepares 42.52 kg and 1.2 kg of silica powder with a particle size of 100 mesh to 150 mesh and a purity of 98% by weight are sent to a mixer and mixed, and stirred evenly;
[0071] The mixture obtained after mixing is sent to a calcination furnace for calcination to form a complex, the calcination temperature is 290°C, and the calcination time is 20 minutes;
[0072] Load the calcined product into the reaction furnace (full volume is 0.08m 3 ), then add 3.92kg of concentrated sulfuric acid with a concentration of 98% by weight in the reaction furnace, heat the reaction furnace to a temperature of about 310°C for reaction, collect and dry the silicon tetrafluoride generated and process it, after calculation, generate tetrafluoroethylene The conversion rate of silicon dioxide was 96.8%, and the purity of silicon tetrafluoride was 99.8% by weight.
PUM
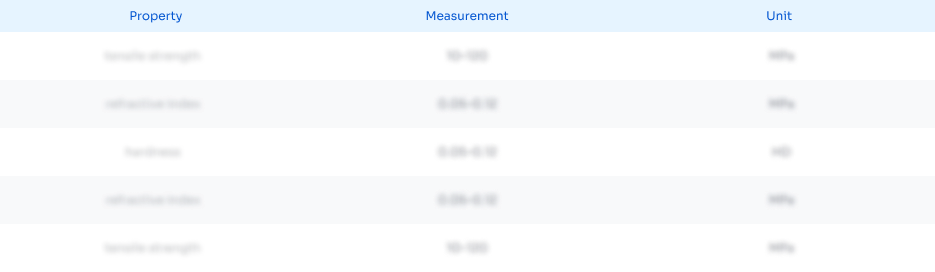
Abstract
Description
Claims
Application Information

- R&D Engineer
- R&D Manager
- IP Professional
- Industry Leading Data Capabilities
- Powerful AI technology
- Patent DNA Extraction
Browse by: Latest US Patents, China's latest patents, Technical Efficacy Thesaurus, Application Domain, Technology Topic, Popular Technical Reports.
© 2024 PatSnap. All rights reserved.Legal|Privacy policy|Modern Slavery Act Transparency Statement|Sitemap|About US| Contact US: help@patsnap.com