Non-polar high polymer film laser moulding method and non-polar high polymer film integral machine for laser processing
A polymer film, non-polar technology, applied in the field of non-polar polymer film laser molding process, can solve the problems of bursting, migration, uneven brightness of laser patterns, etc.
- Summary
- Abstract
- Description
- Claims
- Application Information
AI Technical Summary
Problems solved by technology
Method used
Image
Examples
Embodiment 1 1
[0012] Embodiment 1 All-in-one machine
[0013] Such as figure 1 As shown, it is a schematic diagram of the all-in-one machine integrating laser molding, corona treatment and cooling of the present invention. On the fuselage 1, there are laser molding device 2, corona treatment device 3 and rear forced cooling device 4 in sequence. The cooling device is used for rapid cooling of the non-gradable film after corona treatment.
[0014] The laser molding device 2 and the corona treatment device 3 all adopt the principle and composition of the existing laser molding machine and corona treatment machine, and are used for laser molding and corona treatment on non-polar polymer film substrates. For example figure 2 As shown, the laser molding device consists of a winding system 21, a deflection adjustment roller 22, an unwinding tension roller 23, a preheating roller 24, a laser plate roller 25, a front cooling roller 26, a traction roller 27, a winding tension roller 28 and a wind...
Embodiment 2
[0018] The non-polar polymer film laser molding method of the present invention, its process is "molding+corona+forced cooling→rewinding→aluminum plating→slitting", that is, the non-polar polymer film is laser molded and passed through electric After the corona treatment, the temperature of the film is reduced by forced cooling, which effectively reduces the deformation of the non-polar polymer laser film during the corona process and the distortion of the laser pattern, and then rewinding and aluminum plating, and separation cut.
[0019] The forced cooling can be performed by blowing cold air to the non-polar polymer film, or by contacting the non-polar polymer film after the corona treatment with a cooling roller. The surface temperature of the cooling roll is 5-20°C and can be adjusted.
PUM
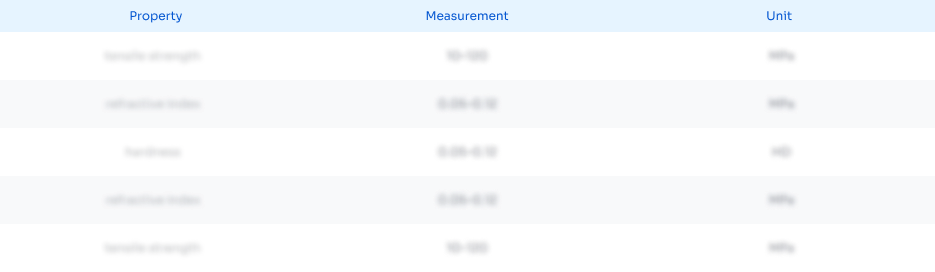
Abstract
Description
Claims
Application Information

- R&D
- Intellectual Property
- Life Sciences
- Materials
- Tech Scout
- Unparalleled Data Quality
- Higher Quality Content
- 60% Fewer Hallucinations
Browse by: Latest US Patents, China's latest patents, Technical Efficacy Thesaurus, Application Domain, Technology Topic, Popular Technical Reports.
© 2025 PatSnap. All rights reserved.Legal|Privacy policy|Modern Slavery Act Transparency Statement|Sitemap|About US| Contact US: help@patsnap.com