Exhaust gas treatment method and incinerator used for steel plate color-coating line
A technology for waste gas treatment and color coating line, which is applied in the field of incinerators and can solve problems such as energy waste, environmental damage, and environmental pollution.
- Summary
- Abstract
- Description
- Claims
- Application Information
AI Technical Summary
Problems solved by technology
Method used
Image
Examples
Embodiment Construction
[0019] In the present invention, the waste gas containing organic solvents generated after heating the steel plate is preheated through a furnace bottom channel and the rear and upper parts of the incinerator, and then enters the incinerator with a furnace temperature of 600-800 ° C, and is passed through contact with gas and combustion-supporting air. For direct combustion, the flow rate of the treated exhaust gas in the incinerator is controlled to be greater than 5 seconds. The length of the combustion channel of the incinerator should ensure that the waste gas stays in it for more than 1 second.
[0020] In order to realize above-mentioned control method, the present invention provides a concrete incinerator embodiment, see Figure 1 to Figure 5 . figure 1 The transverse section structure of the incinerator described in the utility model is illustrated; Figure 2-Figure 4 The cross-sectional structures along the B1-B1, B2-B2, and B3-B3 layers of the incinerator are respe...
PUM
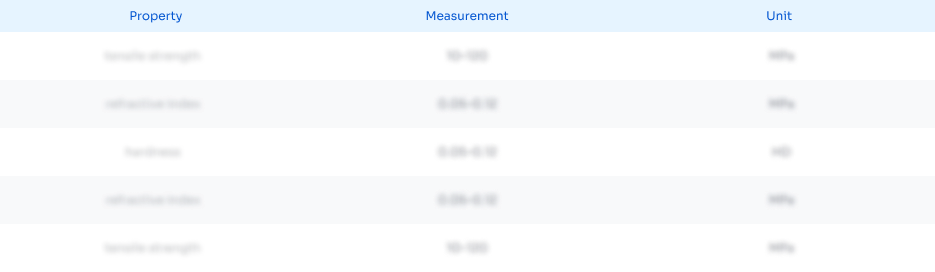
Abstract
Description
Claims
Application Information

- R&D
- Intellectual Property
- Life Sciences
- Materials
- Tech Scout
- Unparalleled Data Quality
- Higher Quality Content
- 60% Fewer Hallucinations
Browse by: Latest US Patents, China's latest patents, Technical Efficacy Thesaurus, Application Domain, Technology Topic, Popular Technical Reports.
© 2025 PatSnap. All rights reserved.Legal|Privacy policy|Modern Slavery Act Transparency Statement|Sitemap|About US| Contact US: help@patsnap.com