Catalytic conversion method for preparing propylene and aromatic hydrocarbons
A catalytic conversion method and propylene technology, applied in the purification/separation of hydrocarbons, chemical instruments and methods, hydrocarbon cracking and hydrocarbon production, etc., can solve the problems of low yield of propylene and aromatics, increase of dry gas and coke yield, etc.
- Summary
- Abstract
- Description
- Claims
- Application Information
AI Technical Summary
Problems solved by technology
Method used
Image
Examples
Embodiment approach 1
[0044] The preferred technical solution of this embodiment comprises the following steps:
[0045] (1) The raw material of type 3 is first contacted with the thermally regenerated catalyst at a reaction temperature of 650°C-800°C and a weight hourly space velocity of 100h -1 -800h -1 , the reaction pressure is 0.10MPa-1.0MPa (absolute pressure), the weight ratio of catalytic cracking catalyst and raw material is 30-150, and the weight ratio of water vapor and raw material is 0.05-1.0 to carry out the cracking reaction;
[0046] (2) The reaction effluent is mixed with the type 2 raw material without oil separation, and the type 2 raw material is mixed at a reaction temperature of 550°C-720°C and a weight hourly space velocity of 10h -1 -300h -1 , the reaction pressure is 0.10MPa-1.0MPa (absolute pressure), the weight ratio of the catalytic cracking catalyst to the raw material is 10-100, and the weight ratio of water vapor to the raw material is 0.05-1.0 to carry out the crac...
Embodiment approach 2
[0053] The preferred technical solution of this embodiment comprises the following steps:
[0054] (1) The raw material of type 3 is first contacted with the thermally regenerated catalyst at a reaction temperature of 650°C-800°C and a weight hourly space velocity of 100h -1 -800h -1 , the reaction pressure is 0.10MPa-1.0MPa (absolute pressure), the weight ratio of catalytic cracking catalyst and raw material is 30-150, and the weight ratio of water vapor and raw material is 0.05-1.0 to carry out the cracking reaction;
[0055] (2) The reaction effluent is mixed with the type 2 raw material without oil separation, and the type 2 raw material is at a reaction temperature of 550°C-720°C, a weight hourly space velocity of 10h-1-300h-1, and a reaction pressure of 0.10MPa-1.0MPa (absolute pressure), the weight ratio of catalytic cracking catalyst and raw material is 10-100, and the cracking reaction is carried out under the condition that the weight ratio of steam and raw material...
Embodiment 1
[0113] This example follows figure 1 process to test. The total height of the pre-lift section, the first reaction zone, the second reaction zone and the third reaction zone of the variable-diameter riser reactor of this process is 21 meters, the diameter of the pre-lift section is 0.25 meters, and its height is 1.5 meters; The first reaction zone has a diameter of 0.25 meters and a height of 3.5 meters; the second reaction zone has a diameter of 0.5 meters and a height of 7 meters; the third reaction zone has a diameter of 1 meter and a height of 9 meters; the first and second reaction zones The longitudinal section of the junction and the junction of the second and third reaction zones etc. should have a trapezoidal apex angle of 45 degrees.
[0114] Feedstock A is directly used as the raw material for catalytic cracking, and the test is carried out on a medium-sized device with a riser reactor. Light aromatics raffinate and C 3 -C 5 Hydrocarbons enter the bottom of reac...
PUM
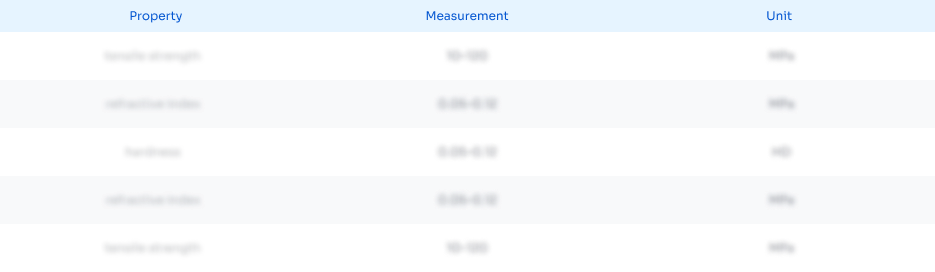
Abstract
Description
Claims
Application Information

- R&D Engineer
- R&D Manager
- IP Professional
- Industry Leading Data Capabilities
- Powerful AI technology
- Patent DNA Extraction
Browse by: Latest US Patents, China's latest patents, Technical Efficacy Thesaurus, Application Domain, Technology Topic, Popular Technical Reports.
© 2024 PatSnap. All rights reserved.Legal|Privacy policy|Modern Slavery Act Transparency Statement|Sitemap|About US| Contact US: help@patsnap.com