Production process and crystallization device for large-particle ammonium sulfate
A technology of production process and crystallization device, which is applied in the field of production process and crystallization device of large-grained ammonium sulfate by pickling method, can solve the problems of uneven particle size of ammonium sulfate product, easy loss of mixing equipment, high energy consumption, etc., and achieve intensified production capacity and operational stability, optimized internal circulation channel, and high internal circulation rate
- Summary
- Abstract
- Description
- Claims
- Application Information
AI Technical Summary
Problems solved by technology
Method used
Image
Examples
Embodiment 1
[0046] The 30% unsaturated ammonium sulfate mother liquor from the pickling tower is sent to the ammonium sulfate crystallizer, where continuous evaporation, concentration and crystallization are carried out, and the evaporation temperature is 40°C. Under the vacuum condition at the top of the crystallizer, 30% of the evaporated water vapor is mixed with the medium-pressure steam by the vacuum jet pump 1, and then pumped to the mother liquor heater to heat the circulating ammonium sulfate mother liquor. The amount of circulating mother liquor entering the external circulation channel is 10 times the feed amount of the raw material inlet of the crystallizer. Through the circulation and concentration of the mother liquor, the ammonium sulfate crystal particles grow continuously, and high-quality ammonium sulfate products with a diameter of 500-2000 μm and a cylindrical shape are obtained. The grown ammonium sulfate crystals are deposited at the bottom of the crystallizer, and ar...
Embodiment 2
[0048] The 50% unsaturated ammonium sulfate mother liquor from the pickling tower is sent to the ammonium sulfate crystallizer, where evaporation, concentration and crystallization are carried out, and the evaporation temperature is 70°C. Under the vacuum condition at the top of the crystallizer, 70% of the evaporated water vapor is mixed with the medium-pressure steam by the vacuum jet pump 1, and then pumped to the mother liquor heater to heat the circulating ammonium sulfate mother liquor. The amount of circulating mother liquor entering the external circulation channel is 40 times the feed amount of the raw material inlet of the crystallizer. Through the circulation and concentration of the mother liquor, the ammonium sulfate crystal particles grow continuously to obtain cylindrical high-quality ammonium sulfate products. The grown ammonium sulfate crystals are deposited at the bottom of the crystallizer, and are pumped to the ammonium sulfate drying and packaging unit wit...
Embodiment 3
[0050] The 43% unsaturated ammonium sulfate mother liquor from the pickling tower is sent to the ammonium sulfate crystallizer, where evaporation, concentration and crystallization are carried out, and the evaporation temperature is 55°C. Under the vacuum condition at the top of the crystallizer, 55% of the evaporated water vapor is mixed with the medium-pressure steam by the vacuum jet pump 1, and then pumped to the mother liquor heater to heat the circulating ammonium sulfate mother liquor. The amount of circulating mother liquor entering the external circulation channel is 25 times the feed amount of the raw material inlet of the crystallizer. Through the circulation and concentration of the mother liquor, the ammonium sulfate crystal particles grow continuously, and high-quality ammonium sulfate products with a diameter of 500-2000 μm and a cylindrical shape are obtained. The grown ammonium sulfate crystals are deposited at the bottom of the crystallizer, and are pumped to...
PUM
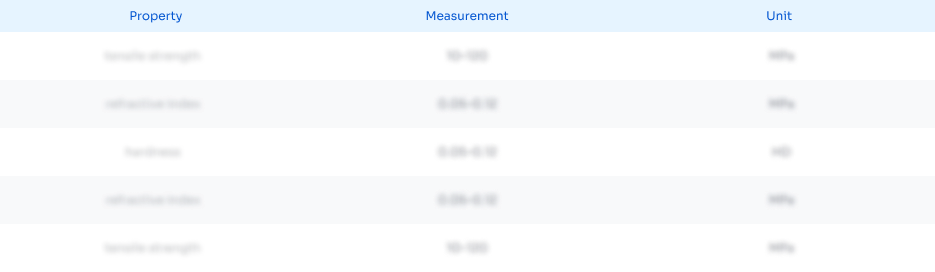
Abstract
Description
Claims
Application Information

- Generate Ideas
- Intellectual Property
- Life Sciences
- Materials
- Tech Scout
- Unparalleled Data Quality
- Higher Quality Content
- 60% Fewer Hallucinations
Browse by: Latest US Patents, China's latest patents, Technical Efficacy Thesaurus, Application Domain, Technology Topic, Popular Technical Reports.
© 2025 PatSnap. All rights reserved.Legal|Privacy policy|Modern Slavery Act Transparency Statement|Sitemap|About US| Contact US: help@patsnap.com