Production process for door curtain material
A production process and door curtain technology, which is applied in the field of chemical industry, can solve the problems of easy dust sticking, harsh use environment, and sticky coating surface, etc., and achieve the effect of superior wear resistance, significant economic value, and long service life
- Summary
- Abstract
- Description
- Claims
- Application Information
AI Technical Summary
Problems solved by technology
Method used
Image
Examples
Embodiment 1
[0031] The specific steps are:
[0032] 1) Sending: The polyester fiber grey cloth (high-strength polyester fiber grey cloth) is placed on the sending device for sending, and one end of the core tube on the sending device is equipped with a magnetic braking device to adjust the tension;
[0033] 2) Preheating and ironing: Preheat and iron the grey fabric on the sending device through the preheating ironing device; this step is a set of heating steel rollers, and the temperature is controlled at 80 degrees to ensure the moisture in the fabric and the low molecular weight contained in the fabric. Volatiles are excluded here to prevent pinholes from affecting air tightness due to volatilization and escape in subsequent coatings;
[0034] 3) Double-sided coating treatment: use a coating machine for padding and vertical scraping, and immerse the preheated and ironed grey cloth into the paste to make the warp and weft of the cloth full of paste, and then pass through a pair of rolle...
Embodiment 2
[0050] The specific steps are:
[0051] 1) Sending: The polyester fiber grey cloth (high-strength polyester fiber grey cloth) is placed on the sending device for sending, and one end of the core tube on the sending device is equipped with a magnetic braking device to adjust the tension;
[0052] 2) Preheating and ironing: preheat and iron the grey fabric on the sending device through the preheating ironing device; this step is a set of heating steel rollers, and the temperature is controlled at 120 degrees to ensure the moisture in the fabric and the low molecular weight contained in the fabric. Volatiles are excluded here to prevent pinholes from affecting air tightness due to volatilization and escape in subsequent coatings;
[0053] 3) Double-sided coating treatment: use a coating machine for padding and vertical scraping, and immerse the preheated and ironed grey cloth into the paste to make the warp and weft of the cloth full of paste, and then pass through a pair of roll...
Embodiment 3
[0070] The specific steps are:
[0071] 1) Sending: The polyester fiber grey cloth (high-strength polyester fiber grey cloth) is placed on the sending device for sending, and one end of the core tube on the sending device is equipped with a magnetic braking device to adjust the tension;
[0072] 2) Preheating and ironing: the grey fabric is preheated and ironed on the sending device through the preheating ironing device; this step is a set of heating steel rollers, and the temperature is controlled at 100 degrees to ensure the moisture in the fabric and the low molecular weight contained in it. Volatiles are excluded here to prevent pinholes from affecting air tightness due to volatilization and escape in subsequent coatings;
[0073] 3) Double-sided coating treatment: use a coating machine for padding and vertical scraping, and immerse the preheated and ironed grey cloth into the paste to make the warp and weft of the cloth full of paste, and then pass through a pair of rolle...
PUM
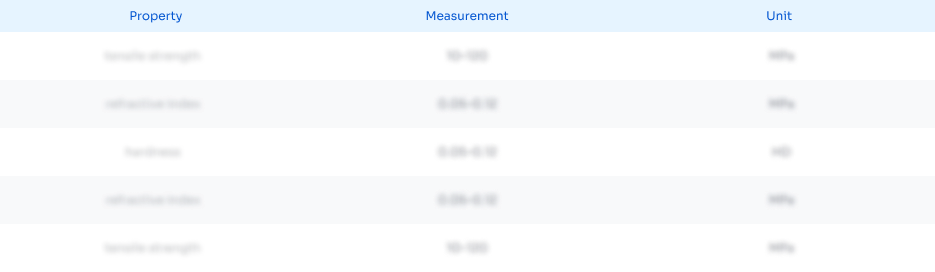
Abstract
Description
Claims
Application Information

- Generate Ideas
- Intellectual Property
- Life Sciences
- Materials
- Tech Scout
- Unparalleled Data Quality
- Higher Quality Content
- 60% Fewer Hallucinations
Browse by: Latest US Patents, China's latest patents, Technical Efficacy Thesaurus, Application Domain, Technology Topic, Popular Technical Reports.
© 2025 PatSnap. All rights reserved.Legal|Privacy policy|Modern Slavery Act Transparency Statement|Sitemap|About US| Contact US: help@patsnap.com