Novel aluminum alloy and heat tinting process for the aluminum alloy product
An aluminum alloy and process technology, applied in the field of aluminum alloy products, can solve the problems of single appearance color, inability to oxidize die-cast aluminum alloy profiles, and difficult coloring, etc., to achieve the effect of enhanced performance and full coating
- Summary
- Abstract
- Description
- Claims
- Application Information
AI Technical Summary
Problems solved by technology
Method used
Examples
Embodiment 1
[0027] Take 80 parts by weight of ADC12 and 20 parts by weight of Al6061, according to the conventional aluminum alloy manufacturing process, put them into the furnace to melt into a liquid state, then put the mixed liquid into the mold for die-casting, take out the profile after die-casting, remove the nozzle, and carry out the process on the profile Post-processing, including conventional processing methods such as peak removal, polishing, grinding and other processing, for future use.
[0028] Perform the following process operations on the processed profiles in turn:
[0029] A. Hanging of the profile, that is, hanging the aluminum alloy profile on a hanger; the hanger can be bent by using a general iron wire. The hanging profile must maintain a certain inclination (> 5°) to facilitate exhaust during electrophoresis or coloring, and reduce spots (bubbles). Points are generated on the decorative surface. Before assembling, place an aluminum sheet between the profile and t...
Embodiment 2
[0040] Take 50 parts by weight of ADC12 and 50 parts by weight of Al6063, according to the conventional aluminum alloy manufacturing process, put them together into a furnace to melt into a liquid state, then put the mixed liquid into the mold for die-casting, take out the profile after die-casting, remove the nozzle, and perform Post-processing, including conventional processing methods such as peak removal, polishing, grinding and other processing, for future use.
[0041] Perform the following process operations on the processed profiles in turn:
[0042] A. Hanging of the profile, that is, hanging the aluminum alloy profile on a hanger; the hanger can be bent by using a general iron wire. The hanging profile must maintain a certain inclination (> 5°) to facilitate exhaust during electrophoresis or coloring, and reduce spots (bubbles). Points are generated on the decorative surface. Before assembling, place an aluminum sheet between the profile and the aluminum screw to p...
Embodiment 3
[0054] Take 45 parts by weight of ADC12 and 55 parts by weight of Al6062, according to the conventional aluminum alloy manufacturing process, put them together into a furnace to melt into a liquid state, then put the mixed liquid into the mold for die-casting, take out the profile after die-casting, remove the nozzle, and perform Post-processing, including conventional processing methods such as peak removal, polishing, grinding and other processing, for future use.
[0055] Perform the following process operations on the processed profiles in turn:
[0056] A. Hanging of the profile, that is, hanging the aluminum alloy profile on a hanger; the hanger can be bent by using a general iron wire. The hanging profile must maintain a certain inclination (> 5°) to facilitate exhaust during electrophoresis or coloring, and reduce spots (bubbles). Points are generated on the decorative surface. Before assembling, place an aluminum sheet between the profile and the aluminum screw to p...
PUM
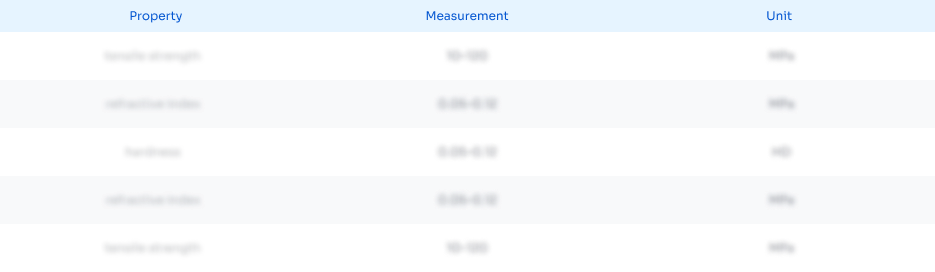
Abstract
Description
Claims
Application Information

- R&D
- Intellectual Property
- Life Sciences
- Materials
- Tech Scout
- Unparalleled Data Quality
- Higher Quality Content
- 60% Fewer Hallucinations
Browse by: Latest US Patents, China's latest patents, Technical Efficacy Thesaurus, Application Domain, Technology Topic, Popular Technical Reports.
© 2025 PatSnap. All rights reserved.Legal|Privacy policy|Modern Slavery Act Transparency Statement|Sitemap|About US| Contact US: help@patsnap.com