Method for reducing positioning torque of stator permanent magnetic type electric machine based on rotor auxiliary slot
A positioning torque and auxiliary groove technology, applied in wind power generation, magnetic circuit static parts, magnetic circuit rotating parts, etc., can solve the problem of increasing the manufacturing cost of the motor and the difficulty of the processing technology, the method of reducing the positioning torque is complex, and the performance of the motor Influence and other problems, to achieve the effect of compact structure, increased manufacturing cost and high power density
- Summary
- Abstract
- Description
- Claims
- Application Information
AI Technical Summary
Problems solved by technology
Method used
Image
Examples
Embodiment Construction
[0015] To figure 1 In the example, the magnetic flux switching doubly salient permanent magnet motor of the present invention includes a stator 1 and a rotor 2. The rotor 2 is located inside or outside the stator 1. Both the stator 1 and the rotor 2 have a doubly salient structure, in which the stator 1 consists of 12 U The stator 1 is composed of three-phase concentrated windings 3 and 12 permanent magnets 4, the rotor 2 has 10 rotor teeth, and each rotor tooth has 2 auxiliary slots 5.
[0016] Since the stator slots are 12 and the rotor teeth are 10, the frequency of the fundamental component of the positioning torque generated is 60, and the corresponding mechanical period is 6 degrees. After the harmonic analysis of the positioning torque of the motor, it is found that the second harmonic of the high-order harmonic components of the positioning torque is relatively large. Therefore, two auxiliary slots are selected on the rotor teeth to weaken the second harmonic component of...
PUM
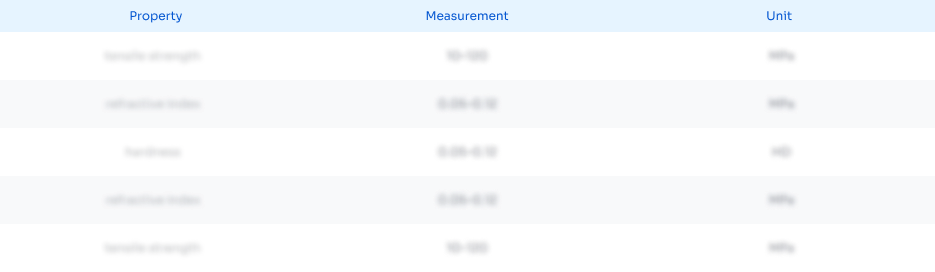
Abstract
Description
Claims
Application Information

- R&D
- Intellectual Property
- Life Sciences
- Materials
- Tech Scout
- Unparalleled Data Quality
- Higher Quality Content
- 60% Fewer Hallucinations
Browse by: Latest US Patents, China's latest patents, Technical Efficacy Thesaurus, Application Domain, Technology Topic, Popular Technical Reports.
© 2025 PatSnap. All rights reserved.Legal|Privacy policy|Modern Slavery Act Transparency Statement|Sitemap|About US| Contact US: help@patsnap.com