Preparation of Ti-6Al-4V titanium alloy large-sized casting ingot
A titanium alloy, large-scale technology, applied in the field of Ti-6Al-4V titanium alloy large-scale ingot preparation, can solve problems such as positive segregation, achieve the effect of stable solidification process, ensure uniformity, and optimize distribution coefficient
- Summary
- Abstract
- Description
- Claims
- Application Information
AI Technical Summary
Problems solved by technology
Method used
Image
Examples
Embodiment 1
[0019] Example 1: (534-20071540 ingot, Φ940mm)
[0020] Step 1 mixing and electrode pressing: according to the composition of the Ti-6Al-4V alloy, select titanium sponge, use Al-V as the intermediate alloy for mixing, and press the electrode block;
[0021] Step 2 Electrode preparation: use the vacuum plasma arc electrode group welding method to prepare the pressed electrode block to obtain a large consumable electrode, and the welding pre-vacuum is ≤ 10Pa;
[0022] Step 3: Vacuum consumable melting once, the crucible is Φ710mm, the melting current is controlled at 18-25KA, and the voltage is controlled at 33-35V;
[0023] Step 4 Secondary vacuum self-consumption smelting smelting, the crucible Φ820mm, the smelting current is controlled at 18-25KA, and the voltage is controlled at 33-35V;
[0024] Step 5 Vacuum consumable smelting of the finished product: crucible Φ940mm, using constant melting rate smelting process, the melting rate control parameter is: 20-23Kg / min; the onl...
Embodiment 2
[0029] Example 2 (534-20071991 ingot, Φ940mm)
[0030] Step 1 mixing and electrode pressing: according to the composition of the Ti-6Al-4V alloy, select titanium sponge, use Al-V as the intermediate alloy for mixing, and press the electrode block;
[0031] Step 2 Electrode preparation: use the vacuum plasma arc electrode group welding method to prepare the pressed electrode block to obtain a large consumable electrode, and the welding pre-vacuum is ≤ 10Pa;
[0032] Step 3: Vacuum self-consumption smelting once, the crucible is Φ710mm, the smelting current is controlled at 23-30KA, and the voltage is controlled at 35-38V;
[0033] Step 4 Secondary vacuum consumable smelting smelting, crucible Φ820mm, smelting current controlled at 23-30KA, voltage controlled at 35-38V;
[0034] Step 5 Vacuum self-consumption melting of finished products: crucible Φ940mm, using constant melting speed melting process, melting speed control parameters: 25 ~ 28Kg / min; online detection system detec...
Embodiment 3
[0038] Example 3 (534-20080688 ingot, Φ1040mm)
[0039] Step 1 mixing and electrode pressing: according to the composition of the Ti-6Al-4V alloy, select titanium sponge, use AL-V as the intermediate alloy for mixing, and press the electrode block;
[0040] Step 2 Electrode preparation: use the vacuum plasma arc electrode group welding method to prepare the pressed electrode block to obtain a large consumable electrode, and the welding pre-vacuum is ≤ 10Pa;
[0041] Step 3: Vacuum self-consumption smelting once, the crucible is Φ820mm, the smelting current is controlled at 30-38KA, and the voltage is controlled at 38-41V;
[0042] Step 4 Secondary vacuum consumable smelting smelting, the crucible Φ940mm, the smelting current is controlled at 30-38KA, and the voltage is controlled at 38-41V;
[0043] Step 5 Vacuum consumable smelting of finished products: Crucible Φ1040mm, using constant melting rate smelting process, melting rate control parameters: 29 ~ 32Kg / min; online dete...
PUM
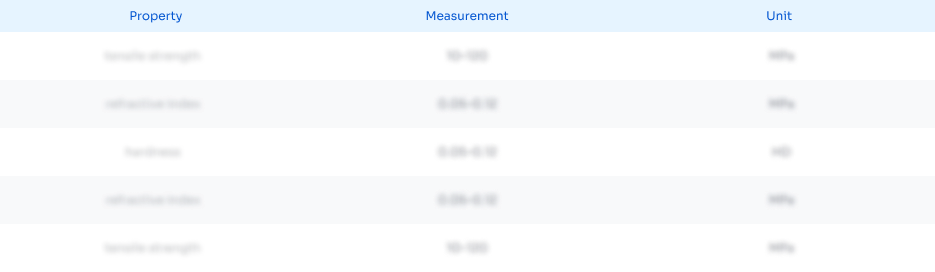
Abstract
Description
Claims
Application Information

- R&D
- Intellectual Property
- Life Sciences
- Materials
- Tech Scout
- Unparalleled Data Quality
- Higher Quality Content
- 60% Fewer Hallucinations
Browse by: Latest US Patents, China's latest patents, Technical Efficacy Thesaurus, Application Domain, Technology Topic, Popular Technical Reports.
© 2025 PatSnap. All rights reserved.Legal|Privacy policy|Modern Slavery Act Transparency Statement|Sitemap|About US| Contact US: help@patsnap.com