Method for making metallic surface pattern
A metal surface and manufacturing method technology, applied in the field of pattern making on metal surfaces, can solve the problems of limited transfer area, inability to achieve discontinuous pattern masking, low efficiency, etc., and achieve the effects of better adaptability and improved pattern transfer efficiency
- Summary
- Abstract
- Description
- Claims
- Application Information
AI Technical Summary
Problems solved by technology
Method used
Image
Examples
Embodiment Construction
[0026] Hereinafter, in conjunction with the accompanying drawings and preferred embodiments, the specific implementation, features, and effects of the method for manufacturing a metal surface pattern proposed in the present invention will be described in detail as follows.
[0027] See figure 1 What is shown is a schematic configuration diagram of an embodiment of the present invention, which is shown as a moment in the process of implementing the method. In the method for making a metal surface pattern in this implementation, the metal surface 1 is an aluminum alloy product surface, the material of which is A1050 (or A1052), the surface is spherical or ellipsoidal, and a layer of photosensitive glue is coated on the metal surface 1 The photosensitive glue layer 3 is formed, and the photosensitive glue used is SY-10 type photosensitive glue provided by Taiwan Liuhe Chemical. The thickness of the photosensitive adhesive layer 3 is 0.5-0.8 mm, the coating area is the entire range of...
PUM
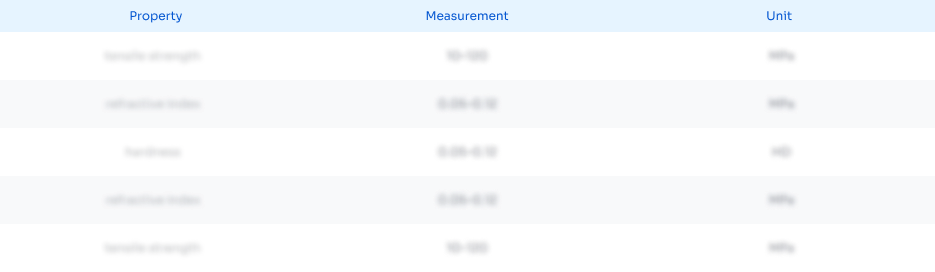
Abstract
Description
Claims
Application Information

- R&D
- Intellectual Property
- Life Sciences
- Materials
- Tech Scout
- Unparalleled Data Quality
- Higher Quality Content
- 60% Fewer Hallucinations
Browse by: Latest US Patents, China's latest patents, Technical Efficacy Thesaurus, Application Domain, Technology Topic, Popular Technical Reports.
© 2025 PatSnap. All rights reserved.Legal|Privacy policy|Modern Slavery Act Transparency Statement|Sitemap|About US| Contact US: help@patsnap.com