Hydrocarbon oil conversion method
A hydrocarbon oil and catalyst technology, applied in chemical instruments and methods, cracking, petroleum industry, etc., can solve the problem of not being able to have high hydrogen yield and hydrocarbon oil conversion rate at the same time, and achieve an increase in production and high hydrogen yield. Effect
- Summary
- Abstract
- Description
- Claims
- Application Information
AI Technical Summary
Problems solved by technology
Method used
Image
Examples
Embodiment 1
[0031] This example is used to illustrate the hydrocarbon oil conversion method provided by the present invention.
[0032] Such as figure 1 As shown, the catalyst is sent to the bottom of the riser reactor 1, hydrocarbon oil 11 and water vapor 12 are added from the bottom of the riser reactor 1, and the catalyst is contacted with the hydrocarbon oil to obtain reaction products and spent catalyst. The reaction conditions in the riser reactor 1 include: the reaction temperature is 480°C, the reaction time is 3 seconds, the weight ratio of catalyst to hydrocarbon oil is 5:1, the reaction pressure is 200 kPa (absolute pressure), water vapor and hydrocarbon The weight ratio of oil is 0.08:1. The coke content of the spent catalyst was 0.95% by weight of the total spent catalyst.
[0033] The reaction product 13 and the unborn catalyst are separated by the settler 2, and then the unborn catalyst is stripped by the stripper 3 and sent to the gasifier 4, and the mixed gas 14 of wate...
Embodiment 2
[0039] This example is used to illustrate the hydrocarbon oil conversion method provided by the present invention.
[0040] The hydrocarbon oil was converted in the same manner as in Example 1, except that the reaction temperature in the gasifier was 660°C. The composition of the synthesis gas is shown in Table 3. The product distribution of the reaction products in riser reactor 1 is shown in Table 4.
[0041] Table 1
[0042] Chemical composition, wt%
al 2 o 3
Na 2 o
Fe 2 o 3
50.0
0.12
0.25 physical properties
Specific surface, m 2 / g
Pore volume, ml / g
Bulk density, g / cm 3
116
0.172
0.80 Metal content, m%
Ni
V
Fe
Ca
Na
Sb
0.62
0.29
0.27
0.056
0.44
0.23 Sieve, volume %
0-20μm
0-40μm
0-80μm
0-110μm
0-149μm
Average particle size, μm
0.4
9.7
56.4
77.8
93.5
74.4
[0043] Table 2
[0044] Density (20℃...
PUM
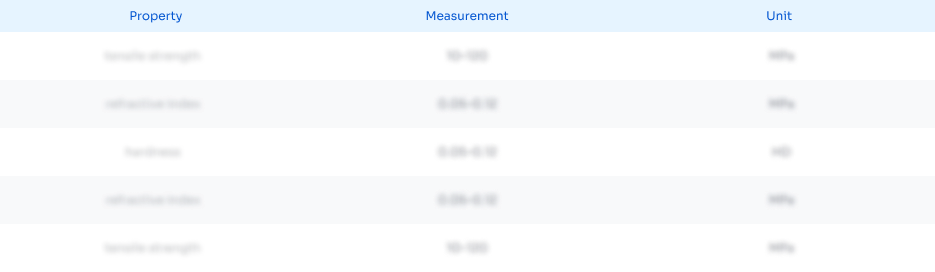
Abstract
Description
Claims
Application Information

- Generate Ideas
- Intellectual Property
- Life Sciences
- Materials
- Tech Scout
- Unparalleled Data Quality
- Higher Quality Content
- 60% Fewer Hallucinations
Browse by: Latest US Patents, China's latest patents, Technical Efficacy Thesaurus, Application Domain, Technology Topic, Popular Technical Reports.
© 2025 PatSnap. All rights reserved.Legal|Privacy policy|Modern Slavery Act Transparency Statement|Sitemap|About US| Contact US: help@patsnap.com