Extruding composite printing ink and preparation method thereof
An extrusion lamination and ink technology, applied in ink, household appliances, applications, etc., can solve the problems of not reaching the composite strength of 1.0N/15mm of packaging products, unfavorable to the health of employees, contamination of food, etc., and achieve good solvent release, The effect of good printing adaptability and strong adhesive fastness
- Summary
- Abstract
- Description
- Claims
- Application Information
AI Technical Summary
Problems solved by technology
Method used
Examples
Embodiment 1
[0047] Preparation:
[0048] a) Dilution process: the modified chlorinated-EVA resin is diluted into a solution with a weight concentration of 20% with a mixed solvent respectively, and the modified chlorinated polypropylene resin is diluted with a weight concentration into a solution with a weight concentration of 20%, and the maleic acid resin is diluted into a solution with a weight concentration of 20%. A solution with a weight concentration of 50%, the mixed solvent is a mixed solvent of ethanol and acetic acid acetic acid, and the weight ratio of ethanol and acetic acid acetic acid is 1.5:1;
[0049] b) Preliminary dispersing process: After stirring the ethanol, acetic acid, dispersant and modified chlorinated-EVA resin liquid accounting for 50% of the total weight, the temperature is raised to 50-60° C., and dispersed for 20 minutes;
[0050] c) Grinding process: after cooling the dispersed material at 30-40°C, grind until the fineness of the material is ≤10 μm;
[005...
Embodiment 2
[0068] Except that formula is following material and parts by weight, all the other are identical with embodiment 1
[0069] Yellow Extrusion Composite Plastic Printing Ink Formulation (weight ratio)
[0070] Modified chlorinated-EVA resin 3
[0071] Modified chlorinated polypropylene resin 2
[0072] Maleic acid resin resin 1
[0073] 2123 Permanent Yellow G 8
[0076] Dispersant 9300 0.1
[0077] Polyethylene wax 0.2
[0078] Matt powder 23D 0.1
[0079] Adhesion Promoter CPO 0.1
[0080] Dry volatile regulator K500 1
[0081] Ethyl acetate 10
[0082] Ethanol 15
[0083] Isopropanol 8
Embodiment 3
[0085] Except that formula is following material and parts by weight, all the other are identical with embodiment 1
[0086] Red extrusion composite plastic printing ink formula (weight ratio)
[0087] Modified chlorinated-EVA resin 8
[0088] Modified chlorinated polypropylene resin 3
[0089] Maleic resin resin 3
[0090] 6B328 red 10
[0093] Dispersant 9300 0.2
[0094] Polyethylene wax 0.5
[0095] Matte powder 23D 0.2
[0096] Adhesion Promoter CPO 0.2
[0097] Dry volatile regulator K500 1.2
[0098] Ethyl acetate 35
[0099] Ethanol 20
[0100] Isopropanol 10
PUM
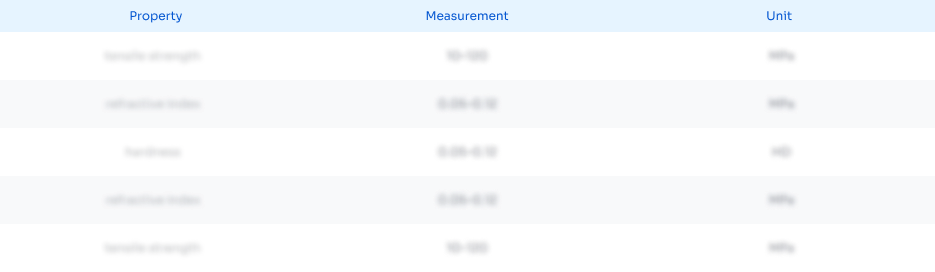
Abstract
Description
Claims
Application Information

- R&D
- Intellectual Property
- Life Sciences
- Materials
- Tech Scout
- Unparalleled Data Quality
- Higher Quality Content
- 60% Fewer Hallucinations
Browse by: Latest US Patents, China's latest patents, Technical Efficacy Thesaurus, Application Domain, Technology Topic, Popular Technical Reports.
© 2025 PatSnap. All rights reserved.Legal|Privacy policy|Modern Slavery Act Transparency Statement|Sitemap|About US| Contact US: help@patsnap.com