Process for preparing chromic oxide by hydrothermal reducing sodium chromate or sodium acid chromate
A technology of sodium dichromate and sodium chromate, applied in the field of inorganic salt industrial production, can solve the problems of high price and high toxicity of low-molecular organic matter, and achieve the effects of low cost, easy filtration and washing, and mild reaction conditions
- Summary
- Abstract
- Description
- Claims
- Application Information
AI Technical Summary
Problems solved by technology
Method used
Examples
Embodiment 1
[0037] In autoclave, add 3000g sodium chromate, 7000g of mother liquor of crystallization, cornstarch 412.5g (according to stoichiometric molar ratio, be 110% of sodium chromate), be heated to 200 ℃, reaction time 2 hours, stirring speed 200rpm, obtain The slurry is easy to filter and separate. The separated chromium hydroxide wet filter cake does not need to be washed or dried, and is directly roasted in a roasting furnace or a rotary kiln at 800-900°C for 2 hours. The cooled chromium oxide is dispersed with a mechanical mill, and the dispersed chromium oxide is turned into a slurry with deionized water at 80°C. The slurry is statically reverse washed 6 times on a mobile disc filter, and the filter cake is at 150-160 °C for 4 hours to obtain the finished chromium oxide. The mother liquor after slurry separation is evaporated and crystallized to obtain solid mixed alkali; the solid mixed alkali is returned to the chromite ore intensified roasting process to realize the recycl...
Embodiment 2
[0039] In the autoclave, add 2000g sodium chromate, crystallization mother liquor 4153g, oxidized starch 300g (according to stoichiometric molar ratio, be 120% of sodium chromate), be heated to 180 ℃, reaction time 3 hours, stirring speed 500rpm, obtain Slurry is easy to filter and separate. The separated chromium hydroxide wet filter cake does not need to be washed or dried, and is directly roasted in a roasting furnace or a rotary kiln at 800-900°C for 2 hours. The cooled chromium oxide is dispersed with a jet mill, and the dispersed chromium oxide is turned into a slurry with deionized water at 85°C. The slurry is statically reverse washed 5 times on a mobile disc filter, and the filter cake is at 150-160 °C for 4 hours to obtain the finished chromium oxide. After the slurry separation, the mother liquor is evaporated, crystallized and separated to obtain a solid mixed alkali; the solid mixed alkali is returned to the chromite ore intensified roasting process to realize th...
Embodiment 3
[0041] Add 1000g sodium dichromate, crystallization mother liquor 1667g, yellow dextrin 200.9g (according to stoichiometric molar ratio, be 130% of sodium dichromate) in autoclave, be heated to 150 ℃, reaction time 3 hours, stirring speed 1200rpm, the resulting slurry is easy to filter and separate. The separated chromium hydroxide wet filter cake does not need to be washed or dried, and is directly roasted in a roasting furnace or a rotary kiln at 800-900°C for 2 hours. The cooled chromium oxide is dispersed with a mechanical mill, and the dispersed chromium oxide is turned into a slurry with deionized water at 90°C. The slurry is statically reverse washed 4 times on a fixed-chamber belt filter, and the filter cake is at 150-160 °C for 4 hours to obtain the finished chromium oxide. After the slurry separation, the mother liquor is evaporated, crystallized and separated to obtain a solid mixed alkali; the solid mixed alkali is returned to the chromite ore intensified roasting...
PUM
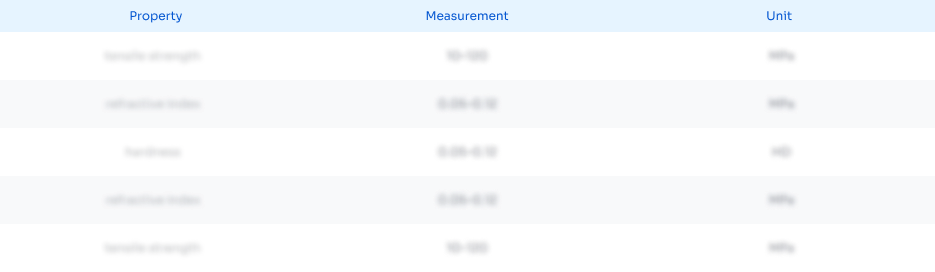
Abstract
Description
Claims
Application Information

- R&D
- Intellectual Property
- Life Sciences
- Materials
- Tech Scout
- Unparalleled Data Quality
- Higher Quality Content
- 60% Fewer Hallucinations
Browse by: Latest US Patents, China's latest patents, Technical Efficacy Thesaurus, Application Domain, Technology Topic, Popular Technical Reports.
© 2025 PatSnap. All rights reserved.Legal|Privacy policy|Modern Slavery Act Transparency Statement|Sitemap|About US| Contact US: help@patsnap.com