Method for preparing methyl alcohol synthesis gas and compressed natural gas from coke oven gas and coal
A technology for compressing natural gas and coke oven gas, which is applied in the direction of gas fuel, fuel, petroleum industry, etc.
- Summary
- Abstract
- Description
- Claims
- Application Information
AI Technical Summary
Problems solved by technology
Method used
Image
Examples
Embodiment 1
[0061] In this embodiment, the method for producing methanol synthesis gas and compressed natural gas by using coke oven gas and coal as raw materials includes the following main steps: coke oven gas undergoes purification treatment, conversion treatment, desulfurization and decarbonization, separation of methane and hydrogen by pressure swing adsorption, and methane-enriched gas Pressurized into compressed natural gas, coal gasification reaction and purification treatment, mixed with hydrogen, fine desulfurization treatment to obtain methanol synthesis gas. Its flowchart is as follows: figure 1 As shown, the specific processing methods of each step are as follows:
[0062] (1), pretreatment of coke oven gas (ie figure 1 coke oven gas pretreatment in
[0063] Using the dry purification temperature swing adsorption method, the raw coke oven gas is subjected to three-stage treatment of rough removal, fine removal, and oil removal to remove most of naphthalene, special sulfur, ...
Embodiment 2
[0097] In this embodiment, the method for producing methanol synthesis gas and compressed natural gas by using coke oven gas and coal as raw materials includes the following main steps: coke oven gas undergoes purification treatment, conversion treatment, desulfurization and decarbonization, separation of methane and hydrogen by pressure swing adsorption, and methane-enriched gas Pressurized into compressed natural gas, coal gasification reaction and purification treatment, mixed with hydrogen, fine desulfurization treatment to obtain methanol synthesis gas. Its flowchart is as follows: figure 1 As shown, the specific processing methods of each step are as follows:
[0098] (1) Pretreatment of coke oven gas
[0099] Using the dry purification temperature swing adsorption method, the raw coke oven gas is subjected to three-stage treatment of rough removal, fine removal, and oil removal to remove most of naphthalene, special sulfur, benzene, HCN, ammonia, and oil to obtain puri...
PUM
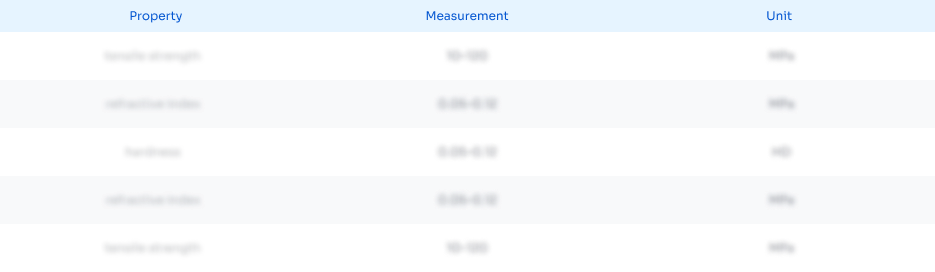
Abstract
Description
Claims
Application Information

- R&D
- Intellectual Property
- Life Sciences
- Materials
- Tech Scout
- Unparalleled Data Quality
- Higher Quality Content
- 60% Fewer Hallucinations
Browse by: Latest US Patents, China's latest patents, Technical Efficacy Thesaurus, Application Domain, Technology Topic, Popular Technical Reports.
© 2025 PatSnap. All rights reserved.Legal|Privacy policy|Modern Slavery Act Transparency Statement|Sitemap|About US| Contact US: help@patsnap.com