Novel method for processing calx sodica sintered alumina by dry method
A technology of sintering alumina and processing methods, which is applied in the field of metallurgy, can solve the problems of low heat production efficiency and large heat consumption, and achieve the effects of reducing heat loss and high economic benefits
- Summary
- Abstract
- Description
- Claims
- Application Information
AI Technical Summary
Problems solved by technology
Method used
Examples
Embodiment Construction
[0025] 1. Raw slurry preparation
[0026] The requirements of our factory ingredients for various raw materials
[0027] 1. Bauxite: particle size <20mm, moisture content less than 7%
[0028] 2. Lime: particle size 75%.
[0029] 3. Soda ash: containing Na2≮58.5%, moisture <2.0%.
[0030] 4. Anthracite: containing Car>50%, Var<25%, Aar<25%, moisture less than 1%
[0031] 5. Drying Bayer process red mud: containing Na20T<10g / 1, containing H20<2%.
[0032] Bauxite, lime, soda ash, anthracite, and carbon are divided into mother liquor in proportion, Ca / (Si+Ti)=2, Na / Al=1, Fe / Al=0.1, the above is the ratio of molecular weight, and coal is 5% , sent to the raw material mill to be ground into raw meal powder, requiring a fineness of 100# and 5% of the sieve.
[0033] 2. Calculation of ingredients
[0034] Al20 Si02 Fe203 Na20 CaO Na2C03 Na2S04 C S Ti02 Ash Bauxite 0.6329 0.0819 0.1162 0.0039 red mud 0.246 0.1552 0.121...
PUM
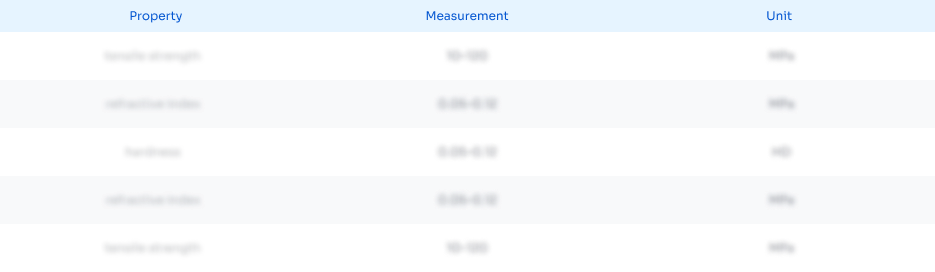
Abstract
Description
Claims
Application Information

- Generate Ideas
- Intellectual Property
- Life Sciences
- Materials
- Tech Scout
- Unparalleled Data Quality
- Higher Quality Content
- 60% Fewer Hallucinations
Browse by: Latest US Patents, China's latest patents, Technical Efficacy Thesaurus, Application Domain, Technology Topic, Popular Technical Reports.
© 2025 PatSnap. All rights reserved.Legal|Privacy policy|Modern Slavery Act Transparency Statement|Sitemap|About US| Contact US: help@patsnap.com