Helix bevel gear active tooth threading machining process
A technology of spiral bevel gear and processing technology, applied in metal processing, metal processing equipment, metal material coating technology, etc., can solve the problems of environmental pollution, low precision, poor appearance, etc., achieve reduction of industrial pollution, high processing efficiency, Reduce the effect of the process flow
- Summary
- Abstract
- Description
- Claims
- Application Information
AI Technical Summary
Problems solved by technology
Method used
Examples
Embodiment 1
[0025] 1. Material selection: 20CrMnTi low-carbon alloy steel is selected as the material, and the outer diameter of the thread is φ36mm; with two positioning holes of φ5mm;
[0026] 2. Heat treatment
[0027] (1) Carburizing and quenching
[0028] The first step: carbon potential 1.2%, temperature 930°C, quenching for 650 minutes;
[0029] Step 2: Diffusion quenching for 90 to 120 minutes, the carbon potential is 0.7%, and the temperature is 910°C to 930°C;
[0030] The third step: keep warm for 45 minutes, the carbon potential is 0.7%, and the temperature is 840°C;
[0031] (2) Tempering
[0032] Temperature 180°C, keep warm for 2 hours;
[0033] (3) Annealing of the threaded part
[0034] The temperature is 600℃~900℃, and the surface hardness of the threaded part after annealing is 28HRC~43HRC;
[0035] 3. Processing
[0036] Fix the above workpiece on the lathe;
[0037] 4. Thread cutting
[0038] Dry cutting is used, the workpiece speed is 601 rpm, the linear spe...
Embodiment 2
[0041] 1. Material selection: The material is 20CrMnTi low-carbon alloy steel, and the outer diameter of the thread is φ36mm; it has two positioning grooves with a length of 10mm, a width of 5mm, and a depth of 8mm;
[0042] 2. Heat treatment
[0043] (1) Carburizing and quenching
[0044] The first step: carbon potential 1.2%, temperature 920°C, quenching for 650 minutes;
[0045] The second step: Diffusion quenching for 90-120 minutes, the carbon potential is 0.7%, and the temperature is 930°C;
[0046] The third step: keep warm for 45 minutes, the carbon potential is 0.7%, and the temperature is 830C;
[0047] (2) Tempering
[0048] Temperature 180°C, keep warm for 2 hours;
[0049] (3) Annealing of the threaded part
[0050] The temperature is 600℃~900℃, and the surface hardness of the threaded part after annealing is 28HRC~43HRC;
[0051] 3. Processing
[0052] Fix the above workpiece on the lathe;
[0053] 4. Thread cutting
[0054] Dry cutting is used, the work...
PUM
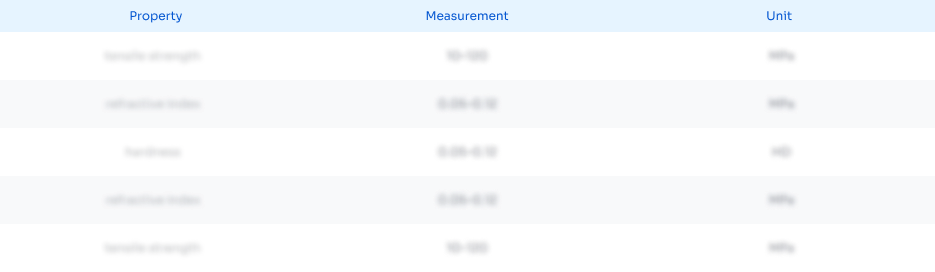
Abstract
Description
Claims
Application Information

- R&D
- Intellectual Property
- Life Sciences
- Materials
- Tech Scout
- Unparalleled Data Quality
- Higher Quality Content
- 60% Fewer Hallucinations
Browse by: Latest US Patents, China's latest patents, Technical Efficacy Thesaurus, Application Domain, Technology Topic, Popular Technical Reports.
© 2025 PatSnap. All rights reserved.Legal|Privacy policy|Modern Slavery Act Transparency Statement|Sitemap|About US| Contact US: help@patsnap.com