Method for producing water-soluble PTC functional conductive carbon paste
A technology of conductive carbon paste and manufacturing method, which is applied to conductive materials dispersed in non-conductive inorganic materials, etc., can solve the problems of oily conductive carbon paste toxicity, restrictions on popularization and application, and impact on human health, etc., and achieves remarkable energy-saving effect. Simple, practical effects
- Summary
- Abstract
- Description
- Claims
- Application Information
AI Technical Summary
Problems solved by technology
Method used
Examples
Embodiment 1
[0029] A kind of manufacture method of water-soluble PTC functional conductive carbon paste, implementation step comprises:
[0030] The first step: the preparation of conductive carbon paste, by weight percentage, using the following raw materials:
[0031] Deionized water 58%, (58g);
[0032] Toner 10%, (10g);
[0033] Two-component polyurethane 24%, (24g);
[0034] Dispersant A: 760W 4%, (4g);
[0035] Dispersant B: 702 4%, (4g);
[0036] At room temperature, gradually add the above-mentioned amount of deionized water into the two-component polyurethane weighed according to the above-mentioned amount, and then add it while stirring; Agent 702, fully stirred evenly, and homogenized with a homogenizer;
[0037] The second step: the preparation of PTC functional materials, by weight percentage, using the following raw materials:
[0038] Deionized water 46%, (46g);
[0039] Substrate wetting agent: 500 3%, (3g);
[0040] Ethylene glycol methyl ether 10%, (10g);
[004...
Embodiment 2
[0050] The first step: the preparation of conductive carbon paste, by weight percentage, using the following raw materials:
[0051] Deionized water 41%, (41g);
[0052] Toner 15%, (15g);
[0053] Two-component polyurethane 28%, (28g);
[0054] Dispersant A: 760W 7%, (7g);
[0055] Dispersant B: 702 9%, (9g);
[0056] At room temperature, gradually add the above-mentioned amount of deionized water into the two-component polyurethane weighed according to the above-mentioned amount, and then add it while stirring; Agent 702, fully stirred evenly, and homogenized with a homogenizer;
[0057] The second step: the preparation of PTC functional materials, by weight percentage, using the following raw materials:
[0058] Deionized water 30%, (30g);
[0059] Substrate wetting agent: 500 2%, (2g);
[0060] Ethylene glycol methyl ether 18%, (18g);
[0061] Stearic Acid 33%, (33g);
[0062] Monoglyceride 10%, (10g);
[0063] Emulsifier: Tween 40 4%, (4g);
[0064]Glycerin 3%, ...
Embodiment 3
[0071] The first step: the preparation of conductive carbon paste, by weight percentage, using the following raw materials:
[0072] Deionized water 40%, (40g);
[0073] Toner 18%, (18g);
[0074] Two-component polyurethane 36%, (36g);
[0075] Dispersant A: 760W 3%, (3g);
[0076] Dispersant B: 702 3%, (3g);
[0077] At room temperature, gradually add the above-mentioned amount of deionized water into the two-component polyurethane weighed according to the above-mentioned amount, and then add it while stirring; Agent 702, uniformly stirred with a high-speed mixer, and then homogenized with a high-speed homogenizer;
[0078] The second step: the preparation of PTC functional materials, by weight percentage, using the following raw materials:
[0079] Deionized Water 32%, (32g)
[0080] Substrate wetting agent: 500 4%, (4g)
[0081] Ethylene glycol methyl ether 12%, (12g);
[0082] Stearic Acid 20%, (20g);
[0083] Monoglycerides 26%, (26g);
[0084] Emulsifier: Tween...
PUM
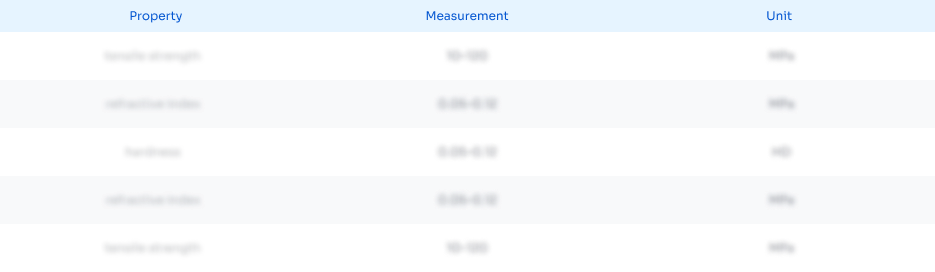
Abstract
Description
Claims
Application Information

- R&D
- Intellectual Property
- Life Sciences
- Materials
- Tech Scout
- Unparalleled Data Quality
- Higher Quality Content
- 60% Fewer Hallucinations
Browse by: Latest US Patents, China's latest patents, Technical Efficacy Thesaurus, Application Domain, Technology Topic, Popular Technical Reports.
© 2025 PatSnap. All rights reserved.Legal|Privacy policy|Modern Slavery Act Transparency Statement|Sitemap|About US| Contact US: help@patsnap.com