Method for device for forming metal micro-thixotropy in semi-solid state assistant by supersonic vibration
A semi-solid metal and ultrasonic vibration technology, applied in the direction of metal processing equipment, etc., can solve the problems of semi-solid metal micro-thixotropy deformation structure shrinkage cavity, non-dense grain structure, low efficiency, etc., to improve micro-thixotropic deformation shape effect, shorten process time, and reduce manufacturing cost
- Summary
- Abstract
- Description
- Claims
- Application Information
AI Technical Summary
Problems solved by technology
Method used
Image
Examples
Embodiment Construction
[0027] like figure 1 and figure 2 As shown, the present invention is provided with a lower mold electric heater 2 at the lower end of the lower mold 10, the lower mold 10 is connected with the ultrasonic horn 1, and the lower mold thermocouple 12 is installed in the lower mold 10, and the lower surface has a fine feature structure The upper end of punch 4 is connected with upper die 8, and upper die 8 upper end is provided with upper die electric heater 6, and upper die 8 is connected with depression bar 7, and upper die thermocouple 9 is installed in upper die 8.
[0028] The lower surface of the punch with the fine characteristic structure is provided with an array of circular holes with a diameter and a depth of 0.8 mm to 1 mm.
[0029] like figure 1 and figure 2 As shown, the specific implementation process of the ultrasonic vibration-assisted semi-solid metal microthixotropic deformation method proposed by the present invention is as follows:
[0030] (1) if figure...
PUM
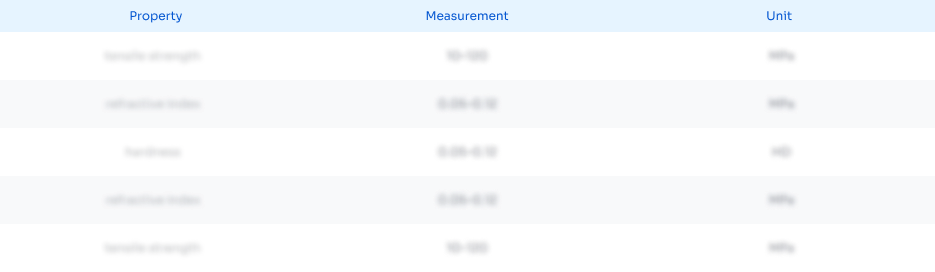
Abstract
Description
Claims
Application Information

- R&D
- Intellectual Property
- Life Sciences
- Materials
- Tech Scout
- Unparalleled Data Quality
- Higher Quality Content
- 60% Fewer Hallucinations
Browse by: Latest US Patents, China's latest patents, Technical Efficacy Thesaurus, Application Domain, Technology Topic, Popular Technical Reports.
© 2025 PatSnap. All rights reserved.Legal|Privacy policy|Modern Slavery Act Transparency Statement|Sitemap|About US| Contact US: help@patsnap.com