Flue gas waste heat recovery method and system for oil and gas boiler
A gas-fired boiler and flue gas waste heat technology, which is applied in the field of flue gas waste heat recovery of oil-fired gas-fired boilers, can solve the problems of large workload, large structure, and difficulty in fully improving heat exchange efficiency, and achieve reduced burden, small size, and favorable The effect of heat and mass exchange
- Summary
- Abstract
- Description
- Claims
- Application Information
AI Technical Summary
Problems solved by technology
Method used
Image
Examples
Embodiment 1
[0036] The waste heat recovery method of the fuel gas boiler flue gas of the present invention comprises the following steps:
[0037] For the first time, before the high-temperature flue gas enters the main cylinder of the waste heat recovery device, the high-temperature flue gas is pre-sprayed and cooled through nozzles in the high-temperature flue gas inlet socket. Among them, the pre-spray cooling is semi-enveloping spraying of the high-temperature flue gas from top to bottom along the radial direction of the high-temperature flue gas inlet pipe seat in the high-temperature flue gas inlet pipe seat.
[0038] Then, the high-temperature flue gas that has been pre-sprayed and cooled enters the main cylinder along the tangential direction of the main cylinder and flows upward while rotating in the main cylinder. The residence time of the flue gas in the main cylinder can be extended to about 2 seconds, which is more conducive to the heat and mass exchange between the flue gas ...
Embodiment 2
[0050] As another kind of scheme of the present invention, other parts are identical with embodiment 1, and difference is:
[0051] The mass flow rate of high-temperature flue gas in the main cylinder is controlled at 2.0kg / (m 2 s) or so.
[0052] Three layers of main spraying devices 3 are arranged in the heat exchange space inside the main cylinder 2, and the nozzles of each layer of main spraying devices 3 are staggered from each other, so that the water mist can cover the heat exchange space with the largest area.
[0053] The pre-spraying device 4 includes three water distribution pipes 41 of the same shape arranged in parallel, the water distribution pipes are arranged on the outer wall of the high-temperature flue gas inlet pipe seat 2, and the opening of the pre-cooling nozzle 42 passes through the through hole provided on the high-temperature flue gas inlet pipe seat 2 Extending to the inside of the high-temperature flue gas inlet pipe seat 2.
Embodiment 3
[0055] As another kind of scheme of the present invention, other parts are identical with embodiment 1, and difference is:
[0056] The mass flow rate of high-temperature flue gas in the main cylinder is controlled at 2.5kg / (m 2 s) or so.
[0057] The distribution main pipe 31, the distribution branch pipe 32 and the atomizing nozzle 33 of the main spraying device 3 are replaced by three shower nozzles distributed in the heat exchange space at intervals. The shower nozzles communicate with the cooling water distribution pipes 16 respectively.
[0058] The mist removal device 5 is a mist eliminator composed of three layers of wire mesh.
[0059] A separate water pump is used to provide cooling water to the pre-spray device 4 .
PUM
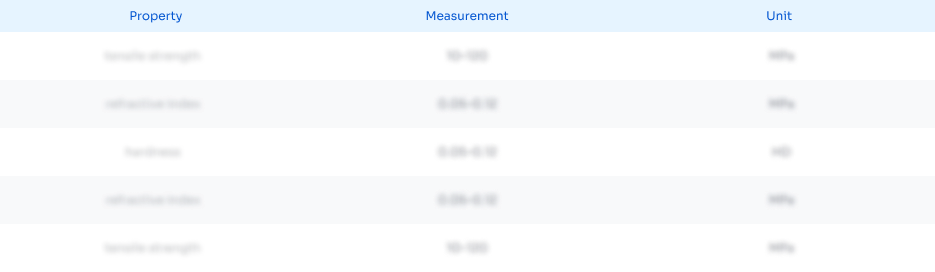
Abstract
Description
Claims
Application Information

- Generate Ideas
- Intellectual Property
- Life Sciences
- Materials
- Tech Scout
- Unparalleled Data Quality
- Higher Quality Content
- 60% Fewer Hallucinations
Browse by: Latest US Patents, China's latest patents, Technical Efficacy Thesaurus, Application Domain, Technology Topic, Popular Technical Reports.
© 2025 PatSnap. All rights reserved.Legal|Privacy policy|Modern Slavery Act Transparency Statement|Sitemap|About US| Contact US: help@patsnap.com