Method for separating caprylic acid from mixture of caprylic acid and capric acid
A separation method and mixture technology, applied in the field of separation of caprylic acid, can solve the problems of high cost, and achieve the effects of facilitating industrial scale-up, low implementation cost and good repeatability
- Summary
- Abstract
- Description
- Claims
- Application Information
AI Technical Summary
Problems solved by technology
Method used
Image
Examples
Embodiment 1
[0028] In a 250ml round bottom flask equipped with a condensing reflux tube, add 10.12g (0.078mol) 2-amino-5-chloropyridine, commercially available octadecyl mixed acid (caprylic acid / capric acid=52.8 / 47.3) 10.03g and 200ml of methanol was heated to reflux for 1h with stirring, and cooled to room temperature. After 2 days, white crystals were obtained, filtered (the filtrate was retained), recrystallized from methanol and filtered to obtain white crystals, washed 3 times with methanol (3×50ml), and dried naturally in the air.
[0029] 13 CNMR (125MHz, CDCl3, TMS): δ=179.53, 159.52, 152.63, 123.55, 111.34, 38.23, 31.52, 29.12, 28.89, 24.84, 22.81, 14.12. m.p. = 37°C.
[0030] The above white crystals were dissolved in 50 ml of 1N hydrochloric acid. A layered liquid was obtained, and the organic layer was octanoic acid (the aqueous phase was retained, and 2-amino-5-chloropyridine was recovered). After washing with 20ml saturated brine, anhydrous Na 2 SO 4 After drying, 4.9...
Embodiment 2
[0035] In a 500ml round bottom flask equipped with a condensing reflux tube, add 10.5g (0.11mol) of 2-aminopyridine, 10.1g of commercially available octadecyl mixed acid (52.8 / 47.3) and 100ml of ethanol, and heat to reflux for 1h under stirring , cooled to room temperature. After 1 day, white crystals were obtained, filtered (the filtrate was retained), recrystallized from methanol, filtered to obtain white crystals, washed 3 times with methanol (3×50ml), and dried naturally in the air. The above white crystals were dissolved in 50 ml of 1N hydrochloric acid to obtain a layered solution, and the organic layer was caprylic acid (the aqueous phase was retained, and 2-aminopyridine was recovered). After washing with 200ml saturated brine, anhydrous Na 2 SO 4 Dry to obtain octanoic acid 4.7g, the yield is 88.1%, and its purity as determined by liquid chromatography is 96.5%.
[0036] 13 CNMR (125MHz, CDCl3, TMS): δ=179.47, 34.26, 31.31, 29.07, 28.88, 24.87, 22.45, 14.12.
[0...
Embodiment 3
[0040]In a 1000ml round bottom flask equipped with a condensing reflux tube, add 42.7g (0.45mol) of 2-hydroxypyridine, 50.0g of commercially available octadecyl mixed acid (52.8 / 47.3) and 500ml of methanol, and heat to reflux for 1h under stirring , cooled to room temperature. After 2 days, white crystals were obtained, filtered (the filtrate was retained), recrystallized from methanol and filtered to obtain white crystals, washed 3 times with methanol (3×50ml), and dried naturally in the air. The above white crystals were dissolved in 500 ml of 1N hydrochloric acid. The layered solution is obtained, and the organic layer is caprylic acid, (the aqueous phase is retained, and 2-hydroxypyridine is recovered). After washing with 100ml saturated brine, anhydrous Na 2 SO 4 After drying, 24.7 g of liquid octanoic acid was obtained with a yield of 94.2%, and its purity was 95.3% as obtained by liquid chromatography.
[0041] 13 CNMR (125MHz, CDCl3, TMS): δ=179.59, 34.38, 31.66, ...
PUM
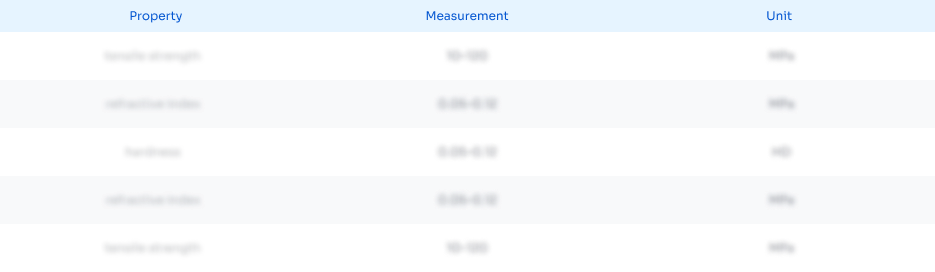
Abstract
Description
Claims
Application Information

- R&D
- Intellectual Property
- Life Sciences
- Materials
- Tech Scout
- Unparalleled Data Quality
- Higher Quality Content
- 60% Fewer Hallucinations
Browse by: Latest US Patents, China's latest patents, Technical Efficacy Thesaurus, Application Domain, Technology Topic, Popular Technical Reports.
© 2025 PatSnap. All rights reserved.Legal|Privacy policy|Modern Slavery Act Transparency Statement|Sitemap|About US| Contact US: help@patsnap.com