Synthesis process for bisphenol acid type epoxy resin with medium molecular mass
A technology of epoxy resin and molecular weight, applied in the field of synthesis technology of bisphenolic acid type epoxy resin with medium molecular weight, can solve the problems of alkali dosage and usage without specific reports, dark product color, etc.
- Summary
- Abstract
- Description
- Claims
- Application Information
AI Technical Summary
Problems solved by technology
Method used
Image
Examples
Embodiment 1
[0021] In a 500mL three-necked flask equipped with a stirrer, a thermometer and a reflux condenser, add 14.3g of bisphenolic acid and 9.3% of epichlorohydrin, then add 0.1g of phase transfer catalyst tetramethylammonium chloride, heat up to 80°C and keep the temperature To react, dissolve the bisphenolic acid, then lower the temperature to 60° C., slowly add 10 mL of 30% liquid caustic soda NaOH dropwise, and finish the reaction after reflux for 3 hours. Recover the unreacted epichlorohydrin under reduced pressure, add organic solvent benzene to dissolve the crude product, then add water to wash until neutral, stand to separate the water layer, and finally distill to remove benzene, which is the bisphenol with molecular weight in the product of the method of the present invention. Acid type epoxy resin, yield 92.5%.
Embodiment 2
[0023] Add 14.3g of bisphenolic acid and 18.6g of epichlorohydrin to a 500mL three-necked flask equipped with a stirrer, a thermometer, and a reflux condenser, then add 0.2g of a phase transfer catalyst tetramethylammonium chloride, and heat up to 70°C Insulate the reaction to dissolve the bisphenolic acid, then lower the temperature to 50° C., slowly add 10 mL of 30% liquid caustic soda NaOH dropwise, and stop the reaction after reflux for 4 hours. Recover the unreacted epichlorohydrin under reduced pressure, add organic solvent benzene to dissolve the crude product, then add water to wash until neutral, stand to separate the water layer, and finally distill to remove benzene, which is the bisphenol with molecular weight in the product of the method of the present invention. Acid type epoxy resin, yield 94.8%.
Embodiment 3
[0025] In a 500mL three-necked flask equipped with a stirrer, a thermometer, and a reflux condenser, add 14.3g of bisphenolic acid and 46.4% of epichlorohydrin, then add 0.2g of a phase transfer catalyst tetramethylammonium chloride, heat up to 70°C and keep the temperature To react, dissolve the bisphenolic acid, then lower the temperature to 60°C, slowly add 30mL of 30% liquid caustic soda NaOH dropwise, and finish the reaction after reflux for 5 hours. Recover the unreacted epichlorohydrin under reduced pressure, add organic solvent benzene to dissolve the crude product, then add water to wash until neutral, stand to separate the water layer, and finally distill to remove benzene, which is the bisphenol with molecular weight in the product of the method of the present invention. Acid type epoxy resin, yield 93.2%.
PUM
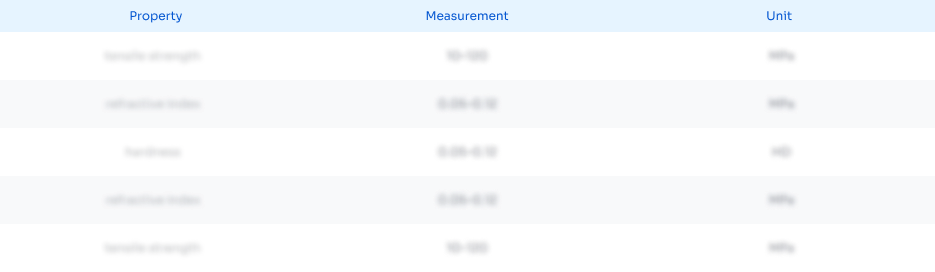
Abstract
Description
Claims
Application Information

- R&D Engineer
- R&D Manager
- IP Professional
- Industry Leading Data Capabilities
- Powerful AI technology
- Patent DNA Extraction
Browse by: Latest US Patents, China's latest patents, Technical Efficacy Thesaurus, Application Domain, Technology Topic, Popular Technical Reports.
© 2024 PatSnap. All rights reserved.Legal|Privacy policy|Modern Slavery Act Transparency Statement|Sitemap|About US| Contact US: help@patsnap.com