Thermal decomposition treatment method for organic castoff
A technology of organic waste and treatment method, which is applied in the field of energy-saving pyrolysis treatment of organic waste, can solve problems such as hindering the popularization of pyrolysis technology, low energy utilization efficiency, and high energy consumption of pyrolysis devices, and achieve an increase in annual operating time, Significant energy-saving effect and reduced pyrolysis energy consumption
- Summary
- Abstract
- Description
- Claims
- Application Information
AI Technical Summary
Problems solved by technology
Method used
Examples
Embodiment 1
[0019] Crushing 50t / d of organic waste for pyrolysis such as waste rubber and plastic, and sending the crushed organic waste for pyrolysis into the feeding port of the feeding device. The feeding device adopts a piston pusher.
[0020] The organic waste for pyrolysis is sent to the pre-pyrolysis device through the piston pusher. The pre-pyrolysis device adopts an externally heated screw conveyor with a hot air jacket, and performs indirect heat exchange with the flue gas in the hot air jacket while conveying the organic waste. Under normal pressure, the pre-pyrolysis time is 1 hour, and the reaction temperature in the pre-pyrolysis section is controlled at 200°C. After being heated, the organic waste undergoes pre-pyrolysis reactions such as drying and preliminary degradation. The waste gas produced in the pre-pyrolysis process is discharged from several waste gas outlets set on the top of the external heating screw conveyor in the pre-pyrolysis section.
[0021] The pre-py...
Embodiment 2
[0025] Send 100t / d of organic waste for pyrolysis such as sludge and oil sludge into the feeding port of the feeding device. The feeding device adopts screw conveyor.
[0026] The organic waste for pyrolysis is sent to the pre-pyrolysis device through the screw conveyor. The pre-pyrolysis unit adopts a scraper machine with a hot-air jacket to carry out indirect heat exchange between the organic waste and the flue gas in the hot-air jacket while conveying. Under normal pressure, the pre-pyrolysis time is 0.5 hour, and the reaction temperature in the pre-pyrolysis section is controlled at 100°C. After the organic waste is heated, it undergoes pre-pyrolysis reactions such as drying and preliminary decomposition. The waste gas generated in the pre-pyrolysis process is discharged from several waste gas outlets on the top of the scraper machine.
[0027] The pre-pyrolysis product enters the pyrolysis section from the material outlet at the tail of the scraper machine in the pre-p...
Embodiment 3
[0031] Sorting and crushing 200t / d domestic waste, the sorted and crushed organic domestic waste is sent to the feeding port of the feeding device. The feeding device adopts scraper machine.
[0032] The organic waste for pyrolysis is sent to the pre-pyrolysis device through the scraper machine. The pre-pyrolysis unit adopts an externally heated piston pusher with a hot air jacket, and performs indirect heat exchange with the flue gas in the hot air jacket while conveying the organic domestic waste. Under normal pressure, the pre-pyrolysis time is 0.1 hour, and the reaction temperature in the pre-pyrolysis section is controlled at 400°C. After being heated, the organic waste undergoes pre-pyrolysis reactions such as drying and preliminary degradation. The waste gas produced in the pre-pyrolysis process is discharged from several waste gas outlets set on the top of the externally heated piston pusher in the pre-pyrolysis section.
[0033] The pre-pyrolysis product enters the...
PUM
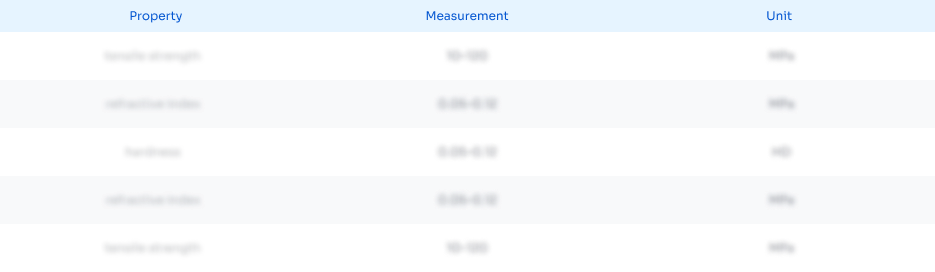
Abstract
Description
Claims
Application Information

- R&D
- Intellectual Property
- Life Sciences
- Materials
- Tech Scout
- Unparalleled Data Quality
- Higher Quality Content
- 60% Fewer Hallucinations
Browse by: Latest US Patents, China's latest patents, Technical Efficacy Thesaurus, Application Domain, Technology Topic, Popular Technical Reports.
© 2025 PatSnap. All rights reserved.Legal|Privacy policy|Modern Slavery Act Transparency Statement|Sitemap|About US| Contact US: help@patsnap.com