Processing technique of split type speed differentiator shell
A differential case and processing technology, which is applied to metal processing equipment, metal processing machinery parts, manufacturing tools, etc., can solve the problem of high rework assembly rate, difficulty in assembling the end face of driven gear and stop beating, and ensure the design requirements and production efficiency Low and other problems, achieve the effect of reducing rear axle noise, high production efficiency, and quality improvement
- Summary
- Abstract
- Description
- Claims
- Application Information
AI Technical Summary
Problems solved by technology
Method used
Image
Examples
Embodiment 1
[0011] Example 1: Taking the processing of the Transit type split differential case as an example, it is to process the two journals ΦD for matching the differential case and the bearing, and the outer circular surface and end face of ΦD1 for matching the driven gear; the outer surface of the assembled bearing is rough The surface roughness value of the assembly driven gear is required to be less than Ra1.6; the surface roughness value of the assembly driven gear is less than Ra1.6; the outer circle runout of the flange facing the two journals is guaranteed to be less than 0.06.
[0012] The clamping and positioning of the Transit differential housing is as follows: the spindle end of the machine tool is matched with the positioning mandrel and the differential housing hole, with a gap of 0.02 to 0.05, and the axial positioning is performed by the small end face of the left housing of the differential; or the self-centering tensioning fixture is used , One end of the tailstock ...
PUM
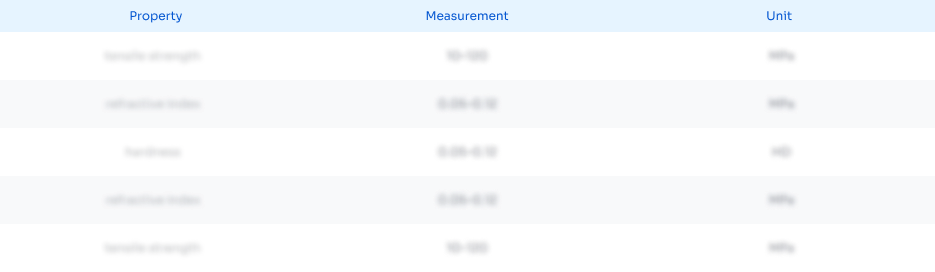
Abstract
Description
Claims
Application Information

- R&D
- Intellectual Property
- Life Sciences
- Materials
- Tech Scout
- Unparalleled Data Quality
- Higher Quality Content
- 60% Fewer Hallucinations
Browse by: Latest US Patents, China's latest patents, Technical Efficacy Thesaurus, Application Domain, Technology Topic, Popular Technical Reports.
© 2025 PatSnap. All rights reserved.Legal|Privacy policy|Modern Slavery Act Transparency Statement|Sitemap|About US| Contact US: help@patsnap.com