Aluminium alloy compression casting pan with compound bottom and compound technique thereof
A technology of aluminum alloy and composite bottom, which is applied to special materials for cooking utensils, cooking utensils, household utensils, etc., and can solve the problems of surface damage, poor positioning reliability, and insufficient flatness of the bottom of the induction cooker, etc.
- Summary
- Abstract
- Description
- Claims
- Application Information
AI Technical Summary
Problems solved by technology
Method used
Image
Examples
Embodiment Construction
[0018] The present invention will be further described below with reference to the accompanying drawings and examples. refer to figure 1 The aluminum alloy die-casting pot with a composite bottom includes an aluminum alloy die-casting pot body 1 and a stainless iron composite bottom sheet 2, and the stainless iron composite bottom sheet 2 is directly laminated and composited with the pot body 1 as a whole. 2 on. refer to figure 2 , the composite bottom aluminum alloy die-casting pot can be manufactured by the following process: first, the aluminum alloy die-casting pot body 1 is die-casted on a die-casting machine; then the surface of the pot body is cleaned; ; Then place the bottom of the aluminum alloy die-casting pot body upside down, and then stick the side of the stainless iron compound film coated with compounding agent on the bottom of the pot body; The bottom sheet is pressed tightly on the bottom of the pot, and the pressing pressure value is kept at 20-100bar; th...
PUM
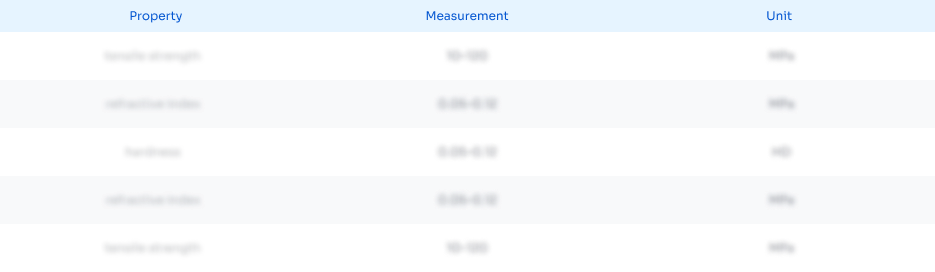
Abstract
Description
Claims
Application Information

- R&D
- Intellectual Property
- Life Sciences
- Materials
- Tech Scout
- Unparalleled Data Quality
- Higher Quality Content
- 60% Fewer Hallucinations
Browse by: Latest US Patents, China's latest patents, Technical Efficacy Thesaurus, Application Domain, Technology Topic, Popular Technical Reports.
© 2025 PatSnap. All rights reserved.Legal|Privacy policy|Modern Slavery Act Transparency Statement|Sitemap|About US| Contact US: help@patsnap.com