Method for measuring coefficient of secondary cooling area for continuous casting
A technology of heat transfer coefficient and measurement method, which is applied in the field of secondary cooling of slab continuous casting, and can solve the problems of one-sided heat transfer coefficient and inability to reflect the comprehensive heat transfer process of the secondary cooling zone.
- Summary
- Abstract
- Description
- Claims
- Application Information
AI Technical Summary
Problems solved by technology
Method used
Image
Examples
Embodiment Construction
[0034] The technical solutions of the present invention will be further described below in conjunction with the accompanying drawings and embodiments.
[0035] see figure 2 As shown, the specific steps of the method for measuring the heat transfer coefficient of the continuous casting secondary cooling zone of the present invention are to first put the thermocouple into the crystallizer, and fix it in the slab, and drag the slab to flow through the secondary cooling zone; The pair measures the temperature of the two temperature measuring points inside the slab, and outputs an electrical signal; then uses the signal processing unit to isolate and amplify the electrical signal, and converts it into a digital signal output; then cuts the cooled slab, and measures the The distance between the temperature measuring points of the two thermocouples inside the slab and the distance between the temperature measuring points on the outside of the slab and the corresponding surface of th...
PUM
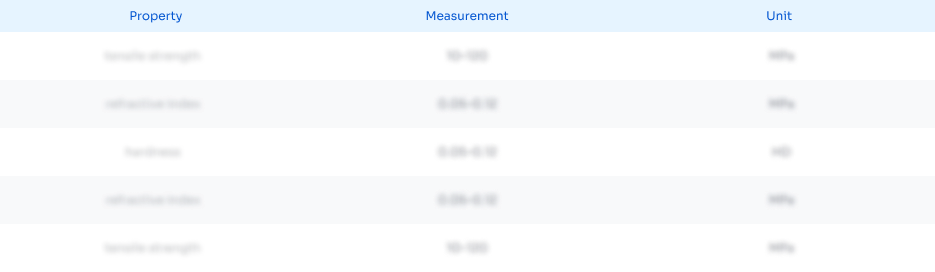
Abstract
Description
Claims
Application Information

- R&D
- Intellectual Property
- Life Sciences
- Materials
- Tech Scout
- Unparalleled Data Quality
- Higher Quality Content
- 60% Fewer Hallucinations
Browse by: Latest US Patents, China's latest patents, Technical Efficacy Thesaurus, Application Domain, Technology Topic, Popular Technical Reports.
© 2025 PatSnap. All rights reserved.Legal|Privacy policy|Modern Slavery Act Transparency Statement|Sitemap|About US| Contact US: help@patsnap.com