Manufacturing process for colored polyester-nylon composite superfine fibre
A technology of ultra-fine fiber and manufacturing process, applied in textiles and papermaking, melt spinning, yarn, etc., can solve the problems of limiting the development speed of new products, inability to dye various patterns, poor chromatogram and color fastness, etc. Significant waterproof and breathable function, good heat fastness, good fluffy effect
- Summary
- Abstract
- Description
- Claims
- Application Information
AI Technical Summary
Problems solved by technology
Method used
Image
Examples
Embodiment Construction
[0017] The present invention will be further described in detail below in conjunction with the accompanying drawings and embodiments.
[0018] Such as figure 1 , the manufacturing process of the colored polyester nylon composite superfine fiber provided by the invention, comprises the following steps:
[0019] (1) Slice the raw materials polyester and nylon to prepare colored masterbatches, wherein the weight ratio of polyester is 70-80 parts, the weight ratio of nylon is 20-30 parts, and the weight ratio of colored masterbatches is 1-10 parts; In the embodiment, polyester is adopted polyester (PET), intrinsic viscosity (IV) is 0.642, and the weight ratio of polyester (PET) accounts for 76wt%; Nylon then adopts nylon 6 (PA6), and relative viscosity is 2.7, and nylon 6 ( The weight ratio of PA6) accounts for 20wt%; the weight ratio of the colored masterbatch accounts for 4wt%, and the intrinsic viscosity (IV) is 0.520;
[0020] (2) Dry the sliced polyester, nylon and colore...
PUM
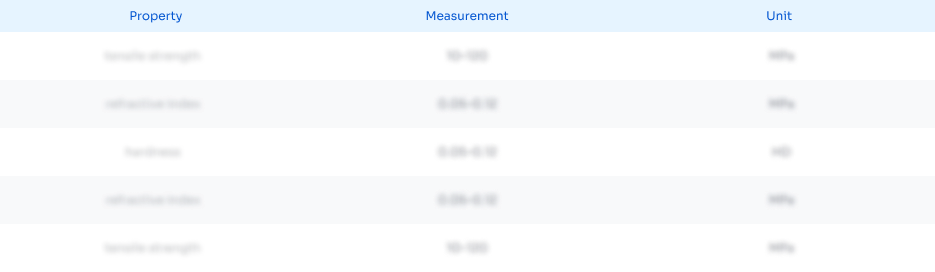
Abstract
Description
Claims
Application Information

- R&D
- Intellectual Property
- Life Sciences
- Materials
- Tech Scout
- Unparalleled Data Quality
- Higher Quality Content
- 60% Fewer Hallucinations
Browse by: Latest US Patents, China's latest patents, Technical Efficacy Thesaurus, Application Domain, Technology Topic, Popular Technical Reports.
© 2025 PatSnap. All rights reserved.Legal|Privacy policy|Modern Slavery Act Transparency Statement|Sitemap|About US| Contact US: help@patsnap.com