Dyeing and finishing process for bamboo fibre
A bamboo fiber, dyeing and finishing technology, applied in the field of textile printing and dyeing, can solve the problems of many production process steps, difficult process control, and large energy consumption, so as to improve the color and gloss, avoid excessive fabric tension, reduce The effect of process control difficulty
- Summary
- Abstract
- Description
- Claims
- Application Information
AI Technical Summary
Problems solved by technology
Method used
Image
Examples
Embodiment Construction
[0027] like figure 1 Shown, the dyeing and finishing process of bamboo fiber comprises the following steps successively:
[0028] Enzyme desizing 1: The weight of the fabric is a, using 7658 amylase at 60°C for padding, then stacking at 60°C for 60 minutes, then fully washing and desizing, the padding liquid rate is 80% to 85%; the concentration of 7658 amylase 8-12g / l. Preferably 10 g / l of 7658 amylase is used.
[0029] Singeing 2: The speed of the machine is 90m / min, and the temperature of the burner is 1100 ℃ ~ 1200 ℃ for two positive and two negative burner singeing, and the singeing series is required to reach level 4 or above.
[0030] Oxygen bleaching 3: Put the fabric into the hydrogen peroxide mixed solution for oxygen bleaching, and then pad and pad at room temperature and steam at 95°C to 100°C for 50 minutes, then wash at least four compartments with hot water at 80°C, the rolling rate of padding at room temperature Between 80% and 85%. The hydrogen peroxide mi...
PUM
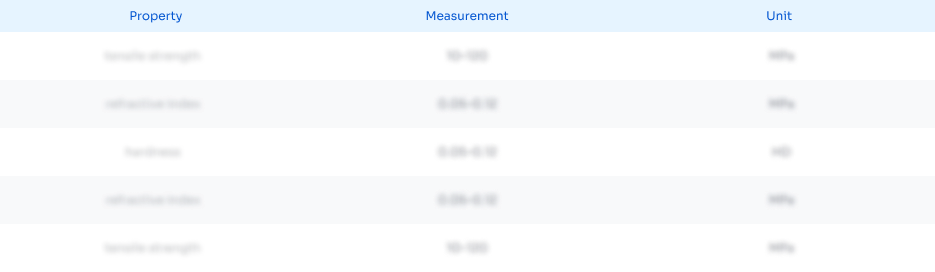
Abstract
Description
Claims
Application Information

- Generate Ideas
- Intellectual Property
- Life Sciences
- Materials
- Tech Scout
- Unparalleled Data Quality
- Higher Quality Content
- 60% Fewer Hallucinations
Browse by: Latest US Patents, China's latest patents, Technical Efficacy Thesaurus, Application Domain, Technology Topic, Popular Technical Reports.
© 2025 PatSnap. All rights reserved.Legal|Privacy policy|Modern Slavery Act Transparency Statement|Sitemap|About US| Contact US: help@patsnap.com